為了保證精密零部件在特殊條件下的正常使用,航空航天、國(guó)防科技和生物醫(yī)療等重要領(lǐng)域?qū)τ诓牧闲阅芴岢隽藰O為苛刻的要求。鈦合金材料同時(shí)兼?zhèn)淞松鲜鲱I(lǐng)域所需的材料性能,具有較強(qiáng)的抗腐蝕能力、較高的比強(qiáng)度、較好的材料韌性以及較強(qiáng)的生物兼容性,繼而成為了應(yīng)用于這些重點(diǎn)領(lǐng)域的重要材料[13]。尤其是在航空航天領(lǐng)域中,鈦合金材料被廣泛應(yīng)用于各種結(jié)構(gòu)件、發(fā)動(dòng)機(jī)零部件、燃?xì)鉁u輪葉片等重要部件中。隨著航空航天的發(fā)展,各部件肩負(fù)的功能日益增多,且結(jié)構(gòu)趨向復(fù)雜化,傳統(tǒng)的材料成型工藝難以快速構(gòu)造出復(fù)雜的結(jié)構(gòu)特征,無(wú)法滿足航空航天領(lǐng)域?qū)τ趶?fù)雜產(chǎn)品快速制備的需求[4]。隨著金屬增材制造技術(shù)趨向成熟,其憑借快速性、低成本、生產(chǎn)周期短和適用性強(qiáng)等優(yōu)勢(shì)[57],為生產(chǎn)加工復(fù)雜零部件提供了新的思路和解決方法。增材制造鈦合金與鍛造鈦合金存在一定的材料性能差異[8],比如硬度、塑性等,這種差別對(duì)后處理加工會(huì)產(chǎn)生一定的影響,對(duì)于推動(dòng)增材制造鈦合金的應(yīng)用同樣也提出了一定的挑戰(zhàn)。為解決這一問(wèn)題,許多學(xué)者針對(duì)增材制造鈦合金展開(kāi)了研究。
Khorasani等[9]使用球頭銑刀對(duì)激光選區(qū)熔化(Selectivelasermelting,SLM)技術(shù)制造的Ti6Al4V假肢髖臼殼的內(nèi)表面進(jìn)行銑削加工,通過(guò)仿真和試驗(yàn)分析了銑刀和工件變形的問(wèn)題。Campos等[10]采用無(wú)涂層的硬質(zhì)合金方頭銑刀對(duì)SLM技術(shù)制備的Ti6Al4V進(jìn)行微細(xì)銑削,并與普通鈦合金樣品進(jìn)行了比較,發(fā)現(xiàn)SLM試驗(yàn)樣品具有更高的強(qiáng)度、硬度,且加工過(guò)后其產(chǎn)生的毛刺更少。戰(zhàn)祥鑫等[11]使用YG類(lèi)硬質(zhì)合金銑刀對(duì)增材制造鈦合金進(jìn)行銑削試驗(yàn),從材料性能、加工流程、加工設(shè)備、加工刀具、加工路徑規(guī)劃和切削參數(shù)等方面進(jìn)行研究,獲得了較好的產(chǎn)品表面質(zhì)量和較優(yōu)的切削參數(shù)。AlRubaie等[12]利用涂有物理氣相沉積(Physicalvapordeposition,PVD)TiAlN涂層的硬質(zhì)合金刀具進(jìn)行銑削試驗(yàn),將常規(guī)鈦合金、SLM鈦合金以及SLM去應(yīng)力鈦合金三者進(jìn)行對(duì)比,試驗(yàn)結(jié)果表明SLM工藝引起的材料微觀組織變化以及硬度和殘余應(yīng)力的增加并沒(méi)有導(dǎo)致材料發(fā)生足夠大的加工行為差異,加工常規(guī)鈦合金的切削參數(shù)同樣適用于SLM制備的鈦合金。雖然金屬增材制造技術(shù)能夠解決復(fù)雜、精密的鈦合金零部件的制備問(wèn)題,但是現(xiàn)有金屬增材制造技術(shù)制備出的零部件通常無(wú)法直接滿足精密產(chǎn)品的應(yīng)用要求,往往需要通過(guò)后處理加工使其達(dá)到所要求的加工尺寸、精度等[13]。微銑削工藝具有材料適用性廣、加工精度高、生產(chǎn)成本低且生產(chǎn)周期短等多種優(yōu)勢(shì),能夠在三維立體表面進(jìn)行復(fù)雜特征的加工,該技術(shù)已經(jīng)成為微切削加工中的重點(diǎn)研究對(duì)象[1415]。并且,在對(duì)鍛造鈦合金進(jìn)行精細(xì)結(jié)構(gòu)加工時(shí),同樣需要微銑削工藝的參與,因此研究不同制造工藝的鈦合金材料的微銑削加工性能對(duì)于推動(dòng)鈦合金材料的進(jìn)一步應(yīng)用具有重要意義。鈦合金材料的導(dǎo)熱率差、切削溫度高且容易使硬質(zhì)合金刀具發(fā)生粘結(jié)磨損,是典型的難加工材料[1618]?,F(xiàn)有的研究發(fā)現(xiàn),傳統(tǒng)的硬質(zhì)合金刀具在加工鈦合金時(shí)存在加工精度較差、刀具壽命過(guò)短以及刀具磨損大等問(wèn)題[1921]。選用超硬材料刀具對(duì)鈦合金進(jìn)行加工是獲取高精度、高質(zhì)量的加工表面的重要手段[22]。聚晶金剛石(Polycrystallinediamond,PCD)刀具依靠耐磨性好、刀具散熱好等優(yōu)勢(shì),成為難加工材料獲取高質(zhì)量加工表面的關(guān)鍵工具[23]。Hao等[24]通過(guò)微銑削試驗(yàn),從表面粗糙度、銑削力和刀具磨損等方面驗(yàn)證了PCD超硬材料微細(xì)銑刀的加工性能優(yōu)于傳統(tǒng)硬質(zhì)合金微細(xì)銑刀。馮素玲等[25]通過(guò)高速銑削鈦合金試驗(yàn),發(fā)現(xiàn)了PCD刀具壽命比硬質(zhì)合金刀具增加了4倍左右,并且能夠獲得更小的表面粗糙度。Wu等[26]對(duì)純鎢進(jìn)行微銑削試驗(yàn),提出PCD刀具可以在更寬的范圍中選擇加工參數(shù)進(jìn)行加工,且PCD刀具的加工質(zhì)量和刀具壽命均要優(yōu)于商用碳化鎢螺旋銑刀。上述的研究都表明,PCD刀具比硬質(zhì)合金刀具更適用于難加工材料的加工。雖然目前已有學(xué)者將增材制造鈦合金與鍛造鈦合金進(jìn)行對(duì)比研究,但多是選用傳統(tǒng)硬質(zhì)合金作為對(duì)比試驗(yàn)的加工刀具。采用超硬材料刀具對(duì)增材制造鈦合金及鍛造鈦合金進(jìn)行加工性能對(duì)比的研究還相對(duì)較少。本文選用PCD微銑刀開(kāi)展了微銑削試驗(yàn),從銑削力、頂端毛刺和表面粗糙度等方面入手,對(duì)比了鍛造鈦合金、SLM鈦合金以及SLM熱處理鈦合金的微銑削加工性能。根據(jù)本研究的試驗(yàn)結(jié)果能夠有針對(duì)性地對(duì)不同制造工藝的鈦合金材料進(jìn)行加工參數(shù)的優(yōu)化,以便獲得更好的加工質(zhì)量。
1、試驗(yàn)設(shè)置
本文選用直徑為1mm的單刃PCD微銑刀作為開(kāi)展微銑削試驗(yàn)的刀具,刀刃長(zhǎng)度為5.5mm,刀具前角為0°,后角為7°,底刃傾角λ為3°,如圖1所示。
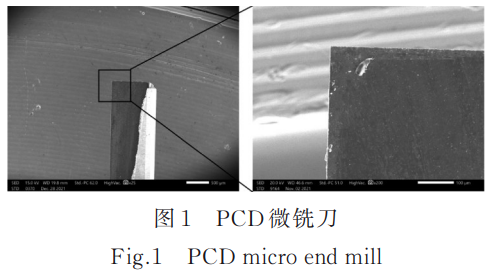
試驗(yàn)前使用基恩士超景深顯微鏡VHX1000檢測(cè)確認(rèn)刀具刃口保持完好,并測(cè)得刀尖圓弧半徑rε為6.9μm,刃口圓弧半徑rβ為7.1μm。本文選用的3種試驗(yàn)材料包括:鍛造的標(biāo)準(zhǔn)鈦合金材料、激光選區(qū)熔化技術(shù)制備的未經(jīng)過(guò)熱處理和經(jīng)過(guò)熱處理的鈦合金材料,本文在后續(xù)將3種不同制造工藝的鈦合金材料分別簡(jiǎn)寫(xiě)為:鍛造、SLM以及SLM熱處理。3種不同制造工藝的鈦合金材料的牌號(hào)均為T(mén)C4,其對(duì)應(yīng)的力學(xué)性能參數(shù)如表1所示。

增材制造鈦合金由飛而康快速制造科技有限責(zé)任公司制備,選用的激光功率為360kW,掃描速度為1700mm/s,粉末粒度直徑為15~53μm。對(duì)增材制造鈦合金的熱處理溫度為800℃,采用室溫冷卻。本試驗(yàn)利用電火花線切割技術(shù)將3種鈦合金材料都切割成尺寸為4mm×10mm×35mm的試驗(yàn)工件,并從左到右按照SLM熱處理鈦合金、SLM鈦合金、鍛造鈦合金的順序?qū)⑵渑挪荚谵D(zhuǎn)接板上,如圖2(a)所示。擺放工件時(shí),根據(jù)打印方向,將兩種增材制造鈦合金材料按照相同的方向進(jìn)行擺放,消除各向異性對(duì)試驗(yàn)結(jié)果的影響。微銑削試驗(yàn)設(shè)置如圖2(b)所示,試驗(yàn)在北京精雕JDGR200T五軸高速加工中心上進(jìn)行,采用Kistler9257B測(cè)力儀對(duì)銑削力進(jìn)行收集,Kistler9257B測(cè)力儀的Fx、Fy、Fz的分辨率均為0.01N。分析銑削力時(shí),首先對(duì)測(cè)得的原始數(shù)據(jù)采用低通濾波,獲得較為穩(wěn)定的力信號(hào),然后在每組銑削力信號(hào)上選取4個(gè)不同的穩(wěn)定切削時(shí)的位置測(cè)量最大值,取平均值作為銑削力的最終測(cè)量結(jié)果。
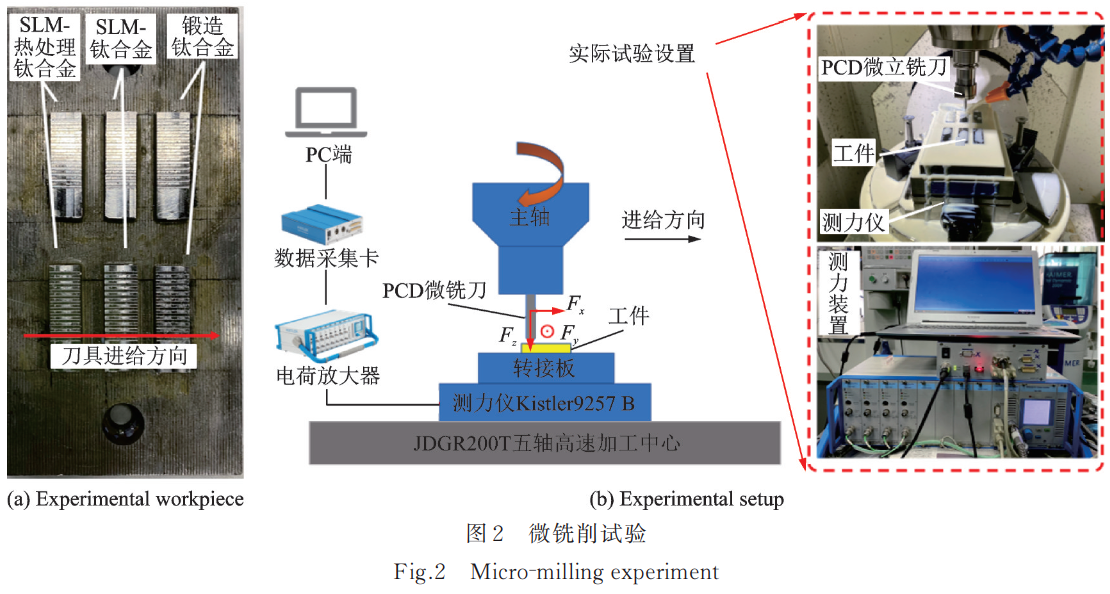
微銑削試驗(yàn)參數(shù)如表2所示,分別選擇4種不同水平的主軸轉(zhuǎn)速、銑削深度和每齒進(jìn)給量對(duì)3種不同制造工藝的鈦合金進(jìn)行單因素微銑削試驗(yàn)。
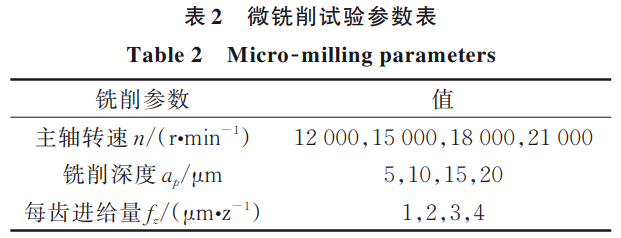
試驗(yàn)全程采用水基切削液進(jìn)行冷卻。每次試驗(yàn)都一次性以相同的銑削參數(shù)對(duì)3種不同制造工藝的鈦合金材料進(jìn)行銑削。為了保證工件擁有良好的平面度,以便精確進(jìn)行試驗(yàn),微銑削試驗(yàn)開(kāi)始前對(duì)所有工件表面進(jìn)行面銑削,確保所有試驗(yàn)工件的高度一致。試驗(yàn)結(jié)束后,將試驗(yàn)工件從工作臺(tái)上拆下,利用基恩士超景深顯微鏡VHX1000對(duì)銑槽頂端毛刺寬度進(jìn)行檢測(cè)。如圖3所示,利用基恩士超景深顯微鏡VH1000測(cè)量頂端毛刺寬度,在銑槽頂端毛刺均勻生成的區(qū)域進(jìn)行檢測(cè),分別選取5個(gè)不同位置測(cè)量,并取平均值作為頂端毛刺寬度測(cè)量的最終結(jié)果。檢測(cè)完頂端毛刺后,將工件超聲清洗干凈,用非接觸式白光干涉光學(xué)輪廓儀ZygoNV7300對(duì)表面粗糙度進(jìn)行測(cè)量。在每條微銑削槽的4個(gè)不同位置,沿刀具進(jìn)給方向進(jìn)行表面粗糙度測(cè)量,測(cè)量時(shí)選取的取樣長(zhǎng)度為0.25mm,取平均值作為表面粗糙度的最終檢測(cè)結(jié)果。
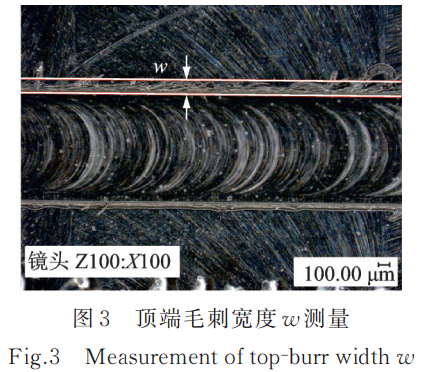
2、試驗(yàn)結(jié)果與討論
2.1 3種不同制造工藝的鈦合金材料的銑削力分析
3種鈦合金材料在不同每齒進(jìn)給量條件下銑削力的變化情況如圖4所示。通過(guò)圖4(a)可以直觀看出,隨著每齒進(jìn)給量的增加,3種材料的銑削力均隨之增大,因?yàn)閱挝粫r(shí)間內(nèi)微銑刀去除的材料量增加,銑削力隨之上漲。其中鍛造鈦合金銑削合力的變化最大,隨著每齒進(jìn)給量從1μm/z增加到4μm/z,鍛造鈦合金的銑削合力從1.19N上漲至4.35N。而SLM鈦合金、SLM熱處理鈦合金的銑削合力分別從1.18、1.74N上升至3.56、3.95N。從圖4(b)可以看出,主銑削力Fy的顯著增大是造成銑削合力快速上漲的主要原因。不難發(fā)現(xiàn),SLM熱處理鈦合金在加工時(shí)的銑削分力在大多數(shù)情況下都要高于其余兩種材料。圖5展示了3種鈦合金材料在不同銑削深度下銑削力的變化情況。從圖5(a)可以看出,軸向力Fz最小,且Fz受到銑削深度的影響最小。隨著銑削深度的加深,鍛造鈦合金、SLM鈦合金以及SLM熱處理鈦合金的Fz分別從1.16、1.14、1.35N上漲至1.51、1.51、1.75N。由于PCD微立銑刀底部存在底刃傾角(λ=3°),該角度是用于減小刀具與已加工表面上發(fā)生彈性回復(fù)的材料的接觸,增強(qiáng)銑削加工的穩(wěn)定性,優(yōu)化加工表面質(zhì)量。當(dāng)?shù)毒吣p較小時(shí),底刃傾角的變化較小,銑削深度的增大并不會(huì)顯著造成與微銑刀底面接觸的工件材料面積增大。因此,在主軸轉(zhuǎn)速和每齒進(jìn)給量不變的條件下,由于銑削深度變化造成Fz的變化幅度較小。銑削合力的變化主要受到主銑削力Fy和進(jìn)給抗力Fx的影響。這是因?yàn)椋娤骷庸ぶ饕窃赬Y平面上去除材料的過(guò)程,F(xiàn)x、Fy是去除材料時(shí)主要的力。圖5(b)能夠直觀地看出,SLM熱處理鈦合金在加工過(guò)程中產(chǎn)生的銑削力明顯大于其余兩種材料。這可能是由于SLM熱處理鈦合金材料的硬度較高,去除材料時(shí)所需的力較大。圖6反映了在不同主軸轉(zhuǎn)速下3種不同制造工藝的鈦材料的銑削力變化情況。通過(guò)圖6(a)能夠看出,隨著主軸轉(zhuǎn)速的加快,不同鈦合金材料的三向銑削力均呈現(xiàn)減小的趨勢(shì)。隨著主軸轉(zhuǎn)速的增大,單位時(shí)間內(nèi)微銑刀去除材料的量減小,進(jìn)而使得銑削力下降。從圖6(b)可以發(fā)現(xiàn),SLM熱處理鈦合金對(duì)于主軸轉(zhuǎn)速的變化最為敏感,隨著主軸轉(zhuǎn)速的加快,銑削力下降幅度最為明顯。當(dāng)主軸轉(zhuǎn)速?gòu)?2000r/min加速至21000r/min時(shí),鍛造鈦合金、SLM鈦合金以及SLM熱處理鈦合金的銑削合力分別從2.18、2.38、3.09N下降至1.56、1.88、2.04N。此外,從圖6中能夠明顯觀察到,鍛造鈦合金的銑削力要明顯小于另外兩種增材制造鈦合金材料。通過(guò)分析不同銑削參數(shù)對(duì)3種鈦合金材料銑削力的影響,能夠發(fā)現(xiàn):總體來(lái)看微銑削加工時(shí)SLM熱處理鈦合金材料的銑削力比鍛造鈦合金和SLM鈦合金的銑削力都要大,且鍛造鈦合金材料的銑削力最小,材料硬度的差異是造成這種情況的重要原因。此外,受到SLM工藝自身缺陷的影響,通過(guò)SLM工藝打印的鈦合金材料未經(jīng)過(guò)熱處理時(shí)會(huì)存在較大的孔隙度,導(dǎo)致材料性能較差[27],而這種情況在材料經(jīng)過(guò)熱處理后會(huì)被改善。有研究表明較大的孔隙度會(huì)引起銑削力的減?。?8],SLM熱處理鈦合金要比SLM鈦合金更為致密,材料孔隙度更小,因此其銑削過(guò)程產(chǎn)生的銑削力更大。
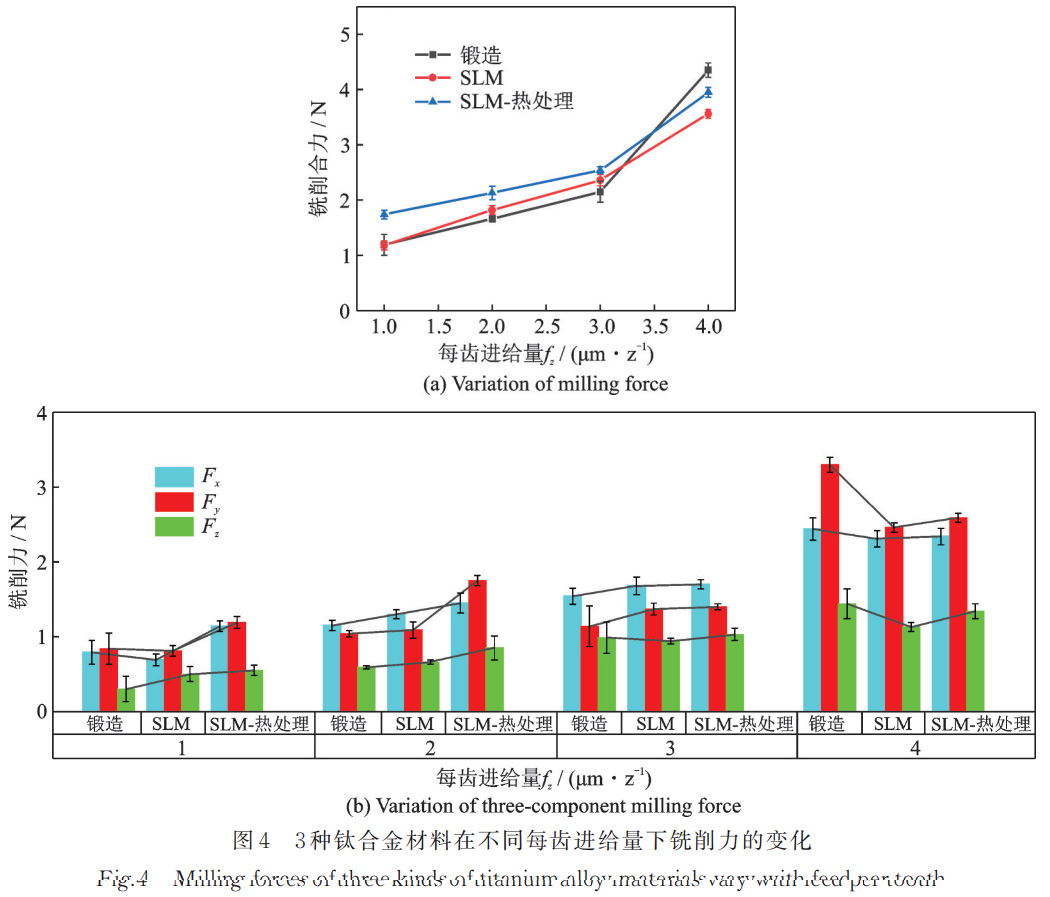
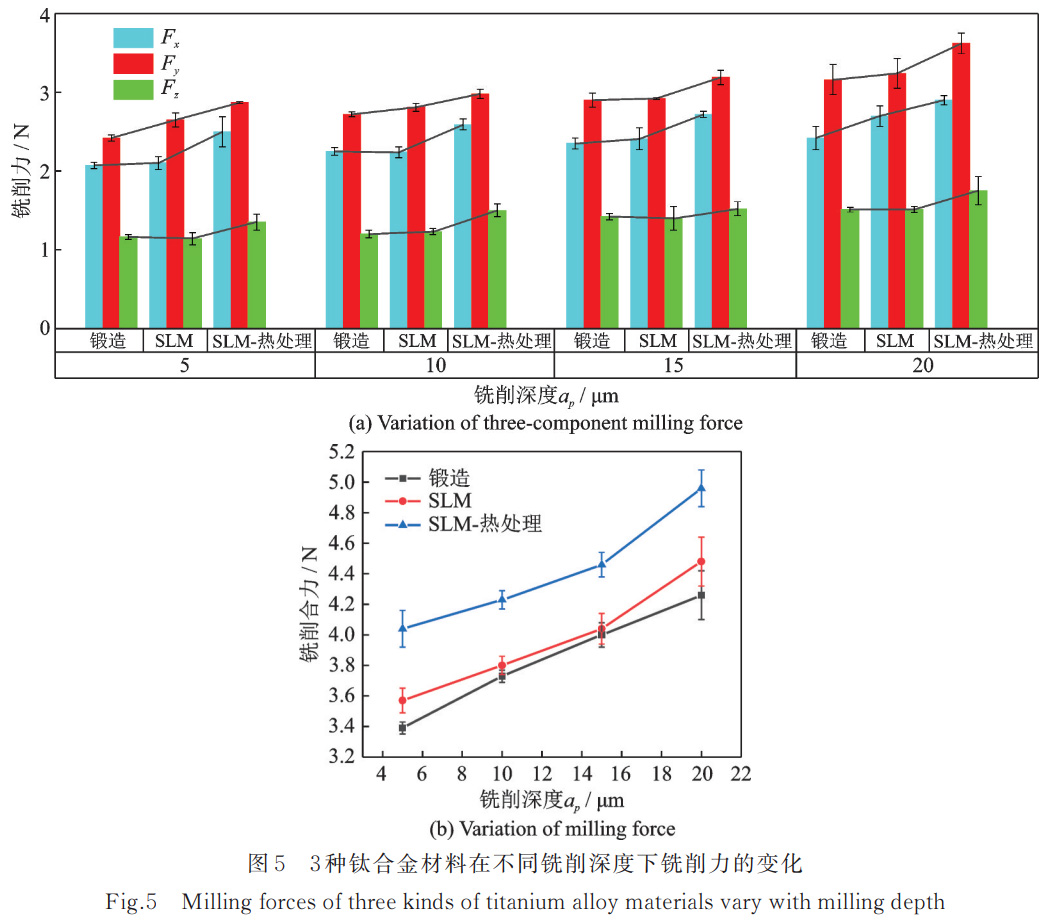
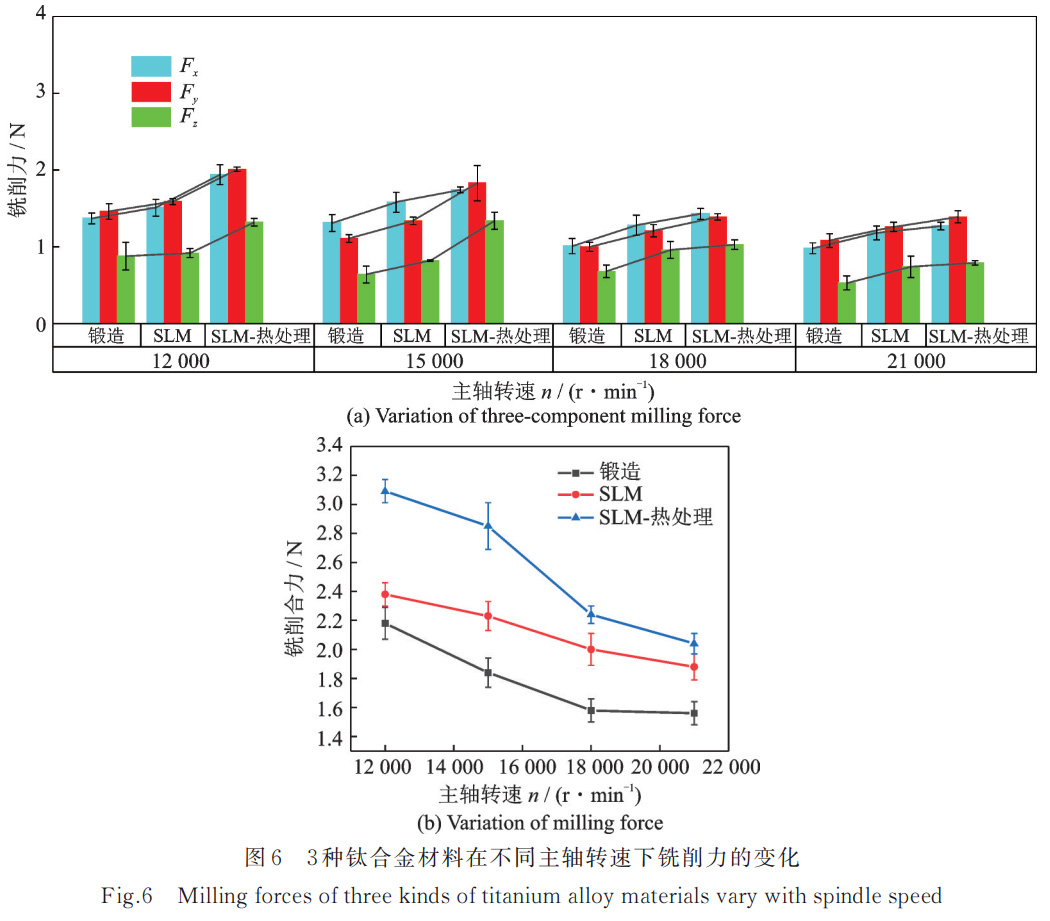
2.2 3種不同制造工藝的鈦合金材料的頂端毛刺分析
毛刺的寬度和高度是評(píng)價(jià)毛刺的參數(shù),由于微銑削毛刺較小,對(duì)測(cè)量工作會(huì)造成一定的困難,為了便于定量分析毛刺規(guī)律,本文選用光學(xué)顯微鏡對(duì)頂端毛刺的寬度進(jìn)行檢測(cè)。圖7為3種鈦合金材料在不同銑削參數(shù)下的頂端毛刺寬度。對(duì)比順銑側(cè)和逆銑側(cè)的頂端毛刺寬度,能夠發(fā)現(xiàn),在不同銑削條件下3種鈦合金材料逆銑側(cè)毛刺尺寸均大于順銑側(cè)毛刺尺寸[10]。

圖8所示為鈦合金材料順逆銑側(cè)頂端毛刺形成機(jī)理差異的示意圖。由于鈦合金材料的塑性較好,在去除材料過(guò)程中工件材料會(huì)發(fā)生較大的塑性變形,在逆銑側(cè),受到未加工表面的阻礙,這部分發(fā)生塑性變形的材料會(huì)產(chǎn)生較大的塑性側(cè)流,本該形成切屑脫落的變形材料演變成較大的毛刺留在了工件頂端。因此在逆銑側(cè),多會(huì)沿著刀具切削刃的旋轉(zhuǎn)和進(jìn)給方向形成尺寸較大的頂端毛刺。而在順銑側(cè),發(fā)生塑性變形的材料會(huì)形成較大的材料堆積,這部分堆積的材料會(huì)隨著刀具切出工件表面時(shí),借助刀具的推動(dòng)作用從工件表面脫落,少數(shù)材料形成尺寸較小的頂端毛刺。觀察圖7(a,b)能夠發(fā)現(xiàn),當(dāng)每齒進(jìn)給量很小時(shí),加工過(guò)程生成的頂端毛刺尺寸較大,這是由于此條件下刀具的瞬時(shí)切削厚度小于材料的最小切削厚度,銑削加工處于負(fù)前角切削狀態(tài),去除材料過(guò)程刀具對(duì)材料的擠壓、犁耕作用嚴(yán)重,增加了材料塑性變形,進(jìn)而促進(jìn)了毛刺的生長(zhǎng)。當(dāng)每齒進(jìn)給量增大,刀具開(kāi)始正常進(jìn)行切割作用,毛刺尺寸先下降,在fz=2μm/z獲得最小值。此處鍛造鈦合金、SLM鈦合金和SLM熱處理鈦合金獲得的逆銑側(cè)最小毛刺寬度分別為184.78、152.3、173.03μm,順銑側(cè)最小毛刺寬度分別為152.89、125.39、139.50μm。隨著進(jìn)給速度的進(jìn)一步加快,刀具單次去除材料量增多,材料變形量增大,毛刺尺寸隨之增長(zhǎng)。圖7(c,d)反映的是銑削深度對(duì)頂端毛刺寬度的影響,隨著銑削深度的增大,3種材料逆銑側(cè)的毛刺寬度也隨之增大,這是由于銑削深度加深,材料去除量增大,切屑的排出受到限制,刀具與工件材料的摩擦、擠壓嚴(yán)重,材料塑性側(cè)流增加,形成較大毛刺。然而,順銑側(cè)毛刺隨著銑削深度的增加先增大,當(dāng)銑削深度ap>10μm,毛刺寬度又開(kāi)始減小。這一現(xiàn)象可能是因?yàn)殂娤魃疃瘸^(guò)了一定的界限切削深度,順銑側(cè)的頂端毛刺形成了尺寸較小的二次毛刺(Ⅱ型毛刺)[2930]。從圖7(e,f)中可以看出,頂端毛刺隨著主軸轉(zhuǎn)速的加快呈現(xiàn)下降的趨勢(shì),說(shuō)明轉(zhuǎn)速的提高有利于減少刀具與材料間擠壓的時(shí)間,有利于減少材料的變形和塑性側(cè)流,抑制頂端毛刺的增長(zhǎng)。觀察圖7可知,在不同銑削條件下SLM鈦合金的頂端毛刺尺寸不論是在順銑側(cè)還是逆銑側(cè)都要小于SLM熱處理鈦合金以及鍛造鈦合金。這可能是因?yàn)镾LM鈦合金的塑性較差,切削時(shí)材料發(fā)生塑性變形的程度較小,且更容易從工件表面脫落,生成的頂端毛刺較小。
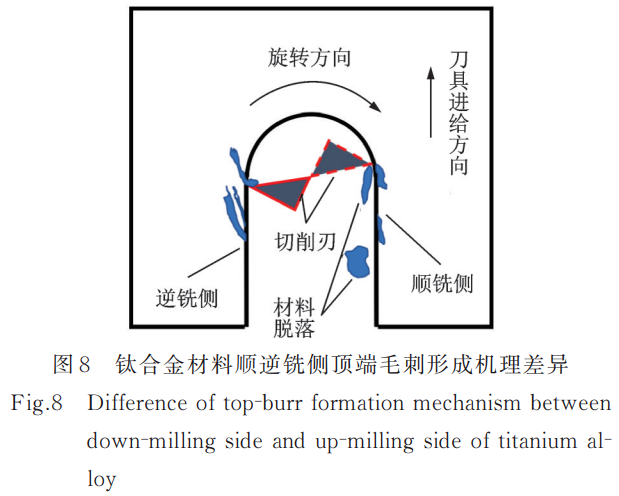
2.3 3種不同制造工藝的鈦合金材料的表面粗糙度分析
不同銑削參數(shù)對(duì)3種鈦合金材料表面粗糙度的影響如圖9所示。如圖9(a)所示,隨著每齒進(jìn)給量的增大,3種鈦合金材料的表面粗糙度均先下降后上升,并在fz=2μm/z獲得最小的表面粗糙度。鍛造鈦合金、SLM鈦合金以及SLM熱處理鈦合金的最小表面粗糙度分別為47.84、65.33、45.69nm。這是由于當(dāng)每齒進(jìn)給量很小時(shí),刀具的瞬時(shí)切削厚度小于最小切削厚度,受到尺寸效應(yīng)的影響,加工過(guò)程的不穩(wěn)定現(xiàn)象增多,此時(shí)的銑刀以滑擦、犁耕去除材料為主,并非正常的切割作用,因此會(huì)導(dǎo)致表面粗糙度較大,獲得的表面質(zhì)量較差。隨著每齒進(jìn)給量的增加,去除材料的作用由最初的擠壓、犁耕轉(zhuǎn)向正常的切割作用,表面粗糙度出現(xiàn)下降趨勢(shì)。隨著進(jìn)給速度的進(jìn)一步加快,瞬時(shí)切削厚度增大,導(dǎo)致銑削力增大,切削過(guò)程不穩(wěn)定現(xiàn)象增加,刀具產(chǎn)生振動(dòng),容易導(dǎo)致表面質(zhì)量變差。
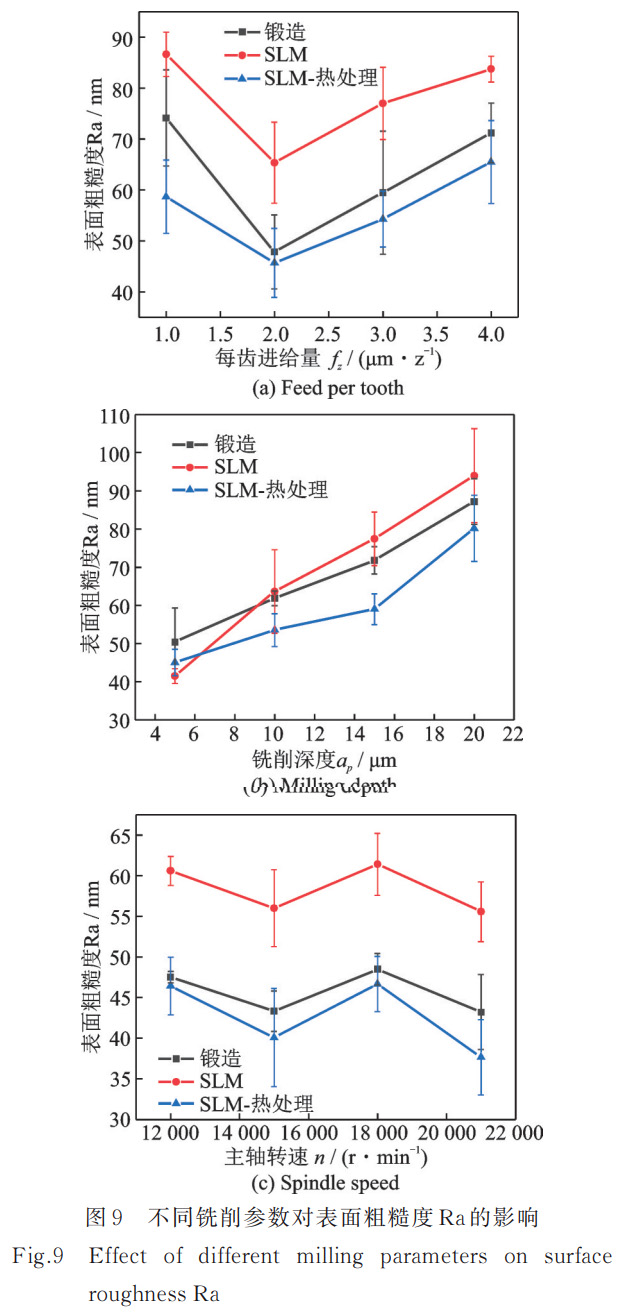
圖9(b)是表面粗糙度受銑削深度影響的變化曲線??梢钥闯?,隨著銑削深度的逐漸增加,微銑槽的表面粗糙度呈上升趨勢(shì)。銑削深度的增加會(huì)導(dǎo)致單位時(shí)間去除的材料量增多,容易導(dǎo)致較大的切削力。以較大銑削深度加工時(shí)刀具容易發(fā)生振動(dòng),導(dǎo)致加工過(guò)程不穩(wěn)定,進(jìn)而影響表面質(zhì)量。圖9(c)是主軸轉(zhuǎn)速對(duì)表面粗糙度的影響,能夠發(fā)現(xiàn)主軸轉(zhuǎn)速加快,表面粗糙度略有下降,但是當(dāng)主軸轉(zhuǎn)速達(dá)到18000r/min時(shí),表面粗糙度又有所上升,這可能是由于較快的轉(zhuǎn)速使得刀具產(chǎn)生振動(dòng),表面粗糙度出現(xiàn)波動(dòng)。通過(guò)對(duì)3種鈦合金材料在不同銑削參數(shù)下表面粗糙度的定量分析,能夠發(fā)現(xiàn),SLM熱處理鈦合金在微銑削加工時(shí)獲得的表面粗糙度要小于鍛造鈦合金和SLM鈦合金。SLM鈦合金在變每齒進(jìn)給量和變主軸轉(zhuǎn)速條件下獲得的表面粗糙度要明顯大于其余兩種材料。鍛造鈦合金在不同銑削參數(shù)下獲得的表面質(zhì)量均處于中等的水平。較高的材料硬度和較低的材料塑性能夠降低加工時(shí)的材料流動(dòng),進(jìn)而獲得更好的表面質(zhì)量[31],因此SLM熱處理鈦合金的表面粗糙度要低于鍛造鈦合金。雖然SLM鈦合金的材料硬度高于鍛造鈦合金,且材料塑性低于鍛造鈦合金,但是由于其孔隙度較大,容易惡化加工后的表面質(zhì)量[32],導(dǎo)致其加工后的表面粗糙度要高于其余兩種鈦合金材料。圖10是3種鈦合金材料在不同每齒進(jìn)給量條件下的表面形貌。當(dāng)fz=1μm/z時(shí),由于刀具對(duì)工件的犁耕作用嚴(yán)重,3種鈦合金材料經(jīng)過(guò)銑削后獲得的表面形貌均較差,表面輪廓曲線變化劇烈。隨著每齒進(jìn)給量增加,在fz=2μm/z時(shí),3種鈦合金材料的表面質(zhì)量有所改善,材料凸起高度變小,表面輪廓曲線變化較為均勻。隨著每齒進(jìn)給量進(jìn)一步增大,3種鈦合金材料的表面形貌又開(kāi)始惡化。通過(guò)整體分析能夠得到,SLM熱處理鈦合金的銑削表面在3種鈦合金材料中最好。相較于鍛造鈦合金和SLM熱處理鈦合金,加工后的SLM鈦合金的表面輪廓曲線變化最為劇烈,獲得的表面質(zhì)量最差。
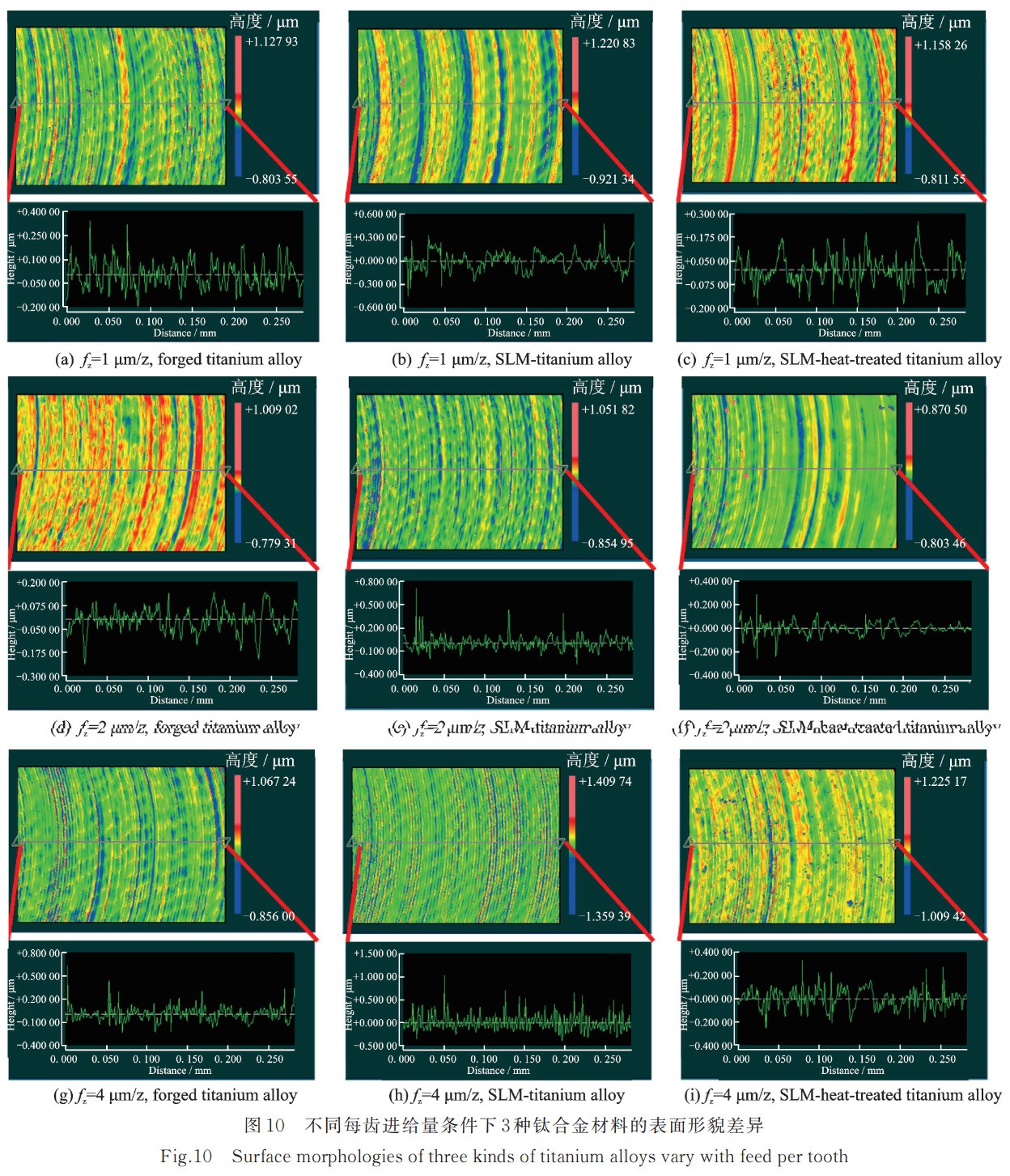
3、結(jié)論
本文以PCD微銑刀作為試驗(yàn)刀具,開(kāi)展了微銑削試驗(yàn)。通過(guò)對(duì)銑削力、頂端毛刺寬度以及表面粗糙度進(jìn)行分析,研究了在不同銑削參數(shù)條件下鍛造鈦合金、SLM鈦合金以及SLM熱處理鈦合金的微銑削加工性能。得到的相關(guān)結(jié)論如下:
(1)微銑削加工時(shí)3種不同制造工藝的鈦合金材料的銑削力變化趨勢(shì)均符合變化規(guī)律。
SLM熱處理鈦合金材料加工產(chǎn)生的銑削力比鍛造鈦合金和SLM鈦合金的銑削力都要大,且鍛造鈦合金材料的銑削力最小。材料硬度的差異是造成這種情況的重要原因。除此之外,SLM鈦合金較大的孔隙度也導(dǎo)致了其銑削力小于SLM熱處理鈦合金。
(2)由于鈦合金材料順逆銑側(cè)頂端毛刺形成機(jī)理的差異,微銑削加工產(chǎn)生的逆銑側(cè)毛刺尺寸均要大于順銑側(cè)毛刺尺寸。在不同銑削條件下SLM鈦合金的頂端毛刺尺寸不論是在順銑側(cè)還是逆銑側(cè)都要小于SLM熱處理鈦合金以及鍛造鈦合金。這是由于SLM鈦合金的塑性較差,切削時(shí)材料發(fā)生塑性變形的程度較小,生成的頂端毛刺較小。
(3)3種不同制造工藝的鈦合金材料的表面粗糙度隨每齒進(jìn)給量增大,呈現(xiàn)先下降后上升的變化規(guī)律,并在fz=2μm/z獲得最小的表面粗糙度。這種現(xiàn)象是受到尺寸效應(yīng)影響的典型結(jié)果。較高的材料硬度和較低的材料塑性能夠降低加工時(shí)的材料流動(dòng),進(jìn)而獲得更好的表面質(zhì)量,因此SLM熱處理鈦合金的表面粗糙度要低于鍛造鈦合金。由于孔隙度較大,容易惡化加工后的表面質(zhì)量,即使SLM鈦合金的硬度高于鍛造鈦合金,且塑性小于鍛造鈦合金,但其加工后的表面粗糙度仍舊較高。
參考文獻(xiàn):
[1] HAO Y, LI S, YANG R. Biomedical titanium alloys and their additive manufacturing[J]. Rare Metals, 2016, 35: 661671.
[2] SINGH P, PUNGOTRA H, KALSI N S. On the characteristics of titanium alloys for the aircraft applica tions[J]. Materials Today: Proceedings, 2017, 4(8): 89718982.
[3] 李梁, 孫健科, 孟祥軍 . 鈦合金的應(yīng)用現(xiàn)狀及發(fā)展前 景[J]. 鈦工業(yè)進(jìn)展, 2004(5): 1924.
LI Liang, SUN Jianke, MENG Xiangjun. Application state and prospects for titanium alloys[J]. Titanium In dustry Progress, 2004(5): 1924.
[4] 李懷學(xué), 鞏水利, 孫帆, 等 . 金屬零件激光增材制造 技 術(shù) 的 發(fā) 展 及 應(yīng) 用[J]. 航 空 制 造 技 術(shù) , 2012, 416(20): 2631.
LI Huaixue, GONG Shuili, SUN Fan, et al. Devel opment and application of laser additive manufacturing for metal component[J]. Aeronautical Manufacturing Technology, 2012, 416(20): 2631.
[5] AHN D. Direct metal additive manufacturing process es and their sustainable applications for green technolo gy: A review[J]. International Journal of Precision Engineering and ManufacturingGreen Technology, 2016, 3: 381395.
[6] TSHEPHE T, AKINWAMIDE S, OLEVSKY E, et al. Additive manufacturing of titaniumbased alloys— A review of methods, properties, challenges, and prospects[J]. Heliyon, 2022, 8(3): e09041.
[7] 朱敏 . 激光增材制造技術(shù)在金屬加工中的應(yīng)用研究 [J]. 世界有色金屬, 2022, 608(20): 232234.
ZHU Min. Application of laser additive manufacturing technology in metal processing[J]. World Nonferrous Metals, 2022, 608(20): 232234.
[8] 梁朝陽(yáng), 張安峰, 梁少端, 等 . 高性能鈦合金激光增 材 制 造 技 術(shù) 的 研 究 進(jìn) 展[J]. 應(yīng) 用 激 光 , 2017, 37(3): 452458.
LIANG Zhaoyang, ZHANG Anfeng, LIANG Shaod uan, et al. Research developments of high-perfor mance titanium alloy by laser additive manufacturing technology[J]. Applied Laser, 2017, 37(3): 452458.
[9] KHORASANI A, GIBSON I, GODARZVAND C, et al. An improved static model for tool deflection in machining of Ti6Al4V acetabular shell produced by selective laser melting[J]. Measurement, 2016, 92: 534544.
[10] CAMPOS F, ARAUJO A, MUNHOZ A, et al. The influence of additive manufacturing on the micromilling machinability of Ti6Al4V: A comparison of SLM and commercial workpieces[J]. Journal of Manufacturing Processes, 2020, 60: 299307.
[11] 戰(zhàn)祥鑫, 熊良釗, 馮晨, 等 . 3D 打印鈦合金結(jié)構(gòu)件銑 削加工技術(shù)[J]. 工具技術(shù), 2020, 54(8): 3840.
ZHAN Xiangxin, XIONG Liangzhao, FENG Chen, et al. Milling technology of 3D printed titanium alloy structure[J]. Tool Engineering, 2020, 54(8): 3840.
[12] ALRUBAIE K, MELOTTI S, RABELO A, et al. Machinability of SLMproduced Ti6Al4V titanium al loy parts[J]. Journal of Manufacturing Processes, 2020, 57: 768786.
[13] MALAKIZADI A, MALLIPEDDI D, DAD BAKHSH S, et al. Postprocessing of additively man ufactured metallic alloys—A review[J]. International Journal of Machine Tools and Manufacture, 2022, 179: 103908.
[14] 張浩, 劉玉德, 石文天, 等 . 微細(xì)切削加工表面質(zhì)量 的研究綜述[J]. 表面技術(shù), 2017, 46(7): 219232.
ZHANG Hao, LIU Yude, SHI Wentian, et al. Quali ty of micro machined surface[J]. Surface Technology, 2017, 46(7): 219232.
[15] ADAMS D P, VASILE M J, BENAVIDES G, et al. Micromilling of metal alloys with focused ion beam-fab ricated tools[J]. Precision Engineering, 2001, 25(2): 107113.
[16] 陳五一, 袁躍峰 . 鈦合金切削加工技術(shù)研究進(jìn)展[J].航空制造技術(shù), 2010, 363(15): 2630.
CHEN Wuyi, YUAN Yuefeng. Research development of cutting technology for titanium alloy[J]. Aeronauti cal Manufacturing Technology, 2010, 363(15): 2630.
[17] 陳爽, 張葆青, 閆石 . 鈦合金加工特性分析及刀具選 擇[J]. 工具技術(shù), 2011, 45(4): 5862.
CHEN Shuang, ZHANG Baoqing, YAN Shi. Analy sis of machining process for titanium alloy and tool selec tion[J]. Tool Engineering, 2011, 45(4): 5862.
[18] 杜敏, 姜增輝, 馮吉路 . 鈦合金切削加工特點(diǎn)及刀具 材料選用[J]. 航空制造技術(shù), 2011, 386(14): 5557.
DU Min, JIANG Zenghui, FENG Jilu. Characteris tics of machining titanium alloys and the choice of tool material[J]. Aeronautical Manufacturing Technology, 2011, 386(14): 5557.
[19] LINDVALL R, LENRICK F, M’SAOUBI R, et al. Performance and wear mechanisms of uncoated ce mented carbide cutting tools in Ti6Al4V machining[J]. Wear, 2021, 477: 203824.
[20] MISHRA S, TALWAR D, SINGH K, et al. Micro mechanical characterization and dynamic wear study of DCArc coated cemented carbide cutting tools for dry titanium turning[J]. Ceramics International, 2021, 47(12): 3179831810.
[21] GHANI J, HARON C, HAMDAN S, et al. Failure mode analysis of carbide cutting tools used for machin ing titanium alloy[J]. Ceramics International, 2013, 39(4): 44494456.
[22] 姜增輝, 董濟(jì)超, 孔繁雅, 等 . 鈦合金銑削加工技術(shù) 研究現(xiàn)狀及發(fā)展[J]. 新技術(shù)新工藝, 2021, 405(9): 5458.
JIANG Zenghui, DONG Jichao, KONG Fanya, et al. Research status and development tendency of titani um alloy milling technology[J]. New Technology & New Process, 2021, 405(9): 5458.
[23] 趙秀香, 曹唯飛, 郭衛(wèi)華 . 超硬材料刀具的特性及應(yīng) 用[J]. 金剛石與磨料磨具工程, 2005(4): 6567.
ZHAO Xiuxiang, CAO Weifei, GUO Weihua. The properties and applications of superhard material cut ting tools[J]. Diamond & Abrasives Engineering, 2005(4): 6567.
[24] HAO X, CHEN M, LIU L, et al. Fabrication of large aspect ratio PCD micromilling tool with pulsed lasers and grinding[J]. Journal of Manufacturing Pro cesses, 2020, 58: 489499.
[25] 馮 素 玲 , 徐 九 華 , 劉 鵬 , 等 . PCD 刀 具 高 速 銑 削TA15 鈦合金的切削性能[J]. 機(jī)械工程材料, 2011, 35(3): 4448
FENG Suling, XU Jiuhua, LIU Peng, et al. Cutting performance of PCD tool during high speed milling of TA15 titanium alloy[J]. Materials for Mechanical En gineering, 2011, 35(3): 4448.
[26] WU W, LI L, HE N, et al. An experimental study on microcutting machining of pure tungsten[J]. Materi als Science Forum, 2012, 1848(723): 377382.
[27] STEF J, POULONQUINTIN A, REDJAIMIA A, et al. Mechanism of porosity formation and influence on mechanical properties in selective laser melting of Ti6Al4V parts[J]. Materials & Design, 2018, 156: 480493.
[28] VARGHESE V, MUJUMDAR S. Micromilling-in duced surface integrity of porous additive manufac tured Ti6Al4V alloy[J]. Procedia Manufacturing, 2021(53): 387394.
[29] 陳鎮(zhèn)宇, 王貴成 . 毛剌的研究現(xiàn)狀及去除技術(shù)[J]. 現(xiàn) 代制造工程, 2004(2): 126128.
CHEN Zhenyu, WANG Guicheng. Studying status of burr and deburring technology[J]. Modern Manufac turing Engineering, 2004(2): 126128.
[30] 王貴成 . 切削方向毛刺生成機(jī)理及其控制[J]. 應(yīng)用 科學(xué)學(xué)報(bào), 1994(3): 239245.
WANG Guicheng. Study on the forming principle and control technology of forward burr[J]. Journal of Ap plied Sciences, 1994(3): 239245.
[31] CHEN W. Cutting forces and surface finish when ma chining medium hardness steel using CBN tools[J]. In ternational Journal of Machine Tools and Manufac ture, 2000(40): 455466.
[32] LI G, CHANDRA S, RASHID R, et al. Machinabil ity of additively manufactured titanium alloys: A com prehensive review[J]. Journal of Manufacturing Pro cesses, 2022, 75: 7299.
相關(guān)鏈接