引言
近年來,鈦合金增材制造技術發(fā)展迅速,尤其是在航空航天、醫(yī)療衛(wèi)生、設備儀器等領域發(fā)揮著重要作用。鈦合金增材制件缺陷的無損檢測是一項重要的研究內容,利用先進的無損檢測裝備和無損檢測技術是確保增材制件質量的主要手段,對未來生產制造行業(yè)具有深遠影響。鑒于無損檢測研究的重要意義,本文作者系統(tǒng)地總結了增材制造合金領域中制件孔隙型缺陷無損檢測技術的研究進展,重點介紹了目前國內外激光超聲技術在增材制件孔隙尺寸和孔隙率檢測中的應用,展望了未來該領域在線無損檢測方向上的發(fā)展動態(tài)。
1、增材制造技術
增材制造(additionmanufacture,AM)技術具有復雜構件快速凈成形、材料利用率高等優(yōu)點,是航空航天領域具代表性顛覆性技術之一[1]。近年來,全球增材制造的市場規(guī)模逐年上升,從行業(yè)方面來看,航空航天領域積累的AM技術方面經驗相對較多[2]。NorskTi-tanium公司報道,飛機上典型的2kg鈦合金部件若采用傳統(tǒng)加工方式需要從30kg原材料上切割完成,相比于該方式,AM技術則僅需6kg的鈦絲,整體來看可為每架波音787飛機節(jié)省約300萬美元。因此,AM技術在國際航空制造領域迅猛發(fā)展,被用來設計更多具有優(yōu)良力學性能或是具有特殊功能的零部件。例如,美國SpaceX太空探索技術公司采用AM技術制造龍飛船發(fā)動機中的SuperDraco推進器,僅用數月時間就完成了發(fā)動機設計和制造,大幅度地節(jié)省了時間成本和原材料成本[3]。此外,美國國家航空航天局研制的低溫熱交換器以及我國的C919客機的主風擋窗框和中央翼根肋等大型復雜結構件亦采用了AM技術[4-5]。
隨著對AM技術深入的研究發(fā)現,由于AM技術在制造過程中材料溫度變化劇烈、成型行為復雜,制造工藝參數以及階梯效應容易對制件的尺寸精度、組織各向異性以及結構完整性產生影響,因而制件內部多發(fā)現氣孔、未熔合、微裂紋等誘發(fā)其疲勞失效的缺陷[6]。國際高溫合金學會主席REED等人分析了高溫合金AM技術需要面對的科學與技術挑戰(zhàn)(如圖1所示),認為目前AM制備產品在質量控制、減少缺陷及產品一致性上仍存在缺少成熟技術的問題,未來需要更多缺陷檢測和性能評價的數據積累,而這離不開數據分析、物理建模、過程仿真、人工智能和新在線檢測技術的支持??捎糜贏M制造過程中的無損檢測手段是未來AM領域科學和工程領域面臨的重要挑戰(zhàn)之一[7]。
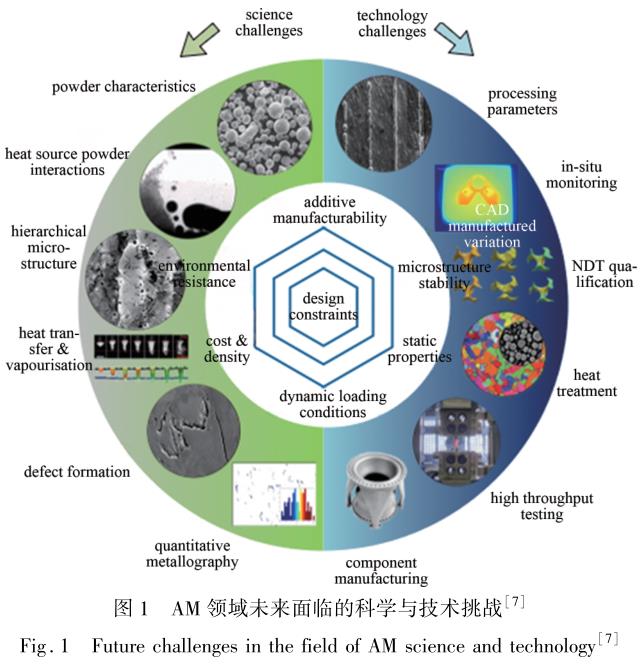
2、孔隙型缺陷的無損檢測技術
隨著AM制件在航空航天等領域逐漸投入使用,對于制件的力學性能等也提出了更高的要求,通過控制制件內孔隙的形成來提高其力學性能的方式引起了該領域研究人員的關注。目前制件內部冶金缺陷的有效控制尚未完全解決,有研究者認為其關鍵在于AM過程中制件組織及缺陷形成規(guī)律尚未完全厘清,且缺少能夠實時觀測其形成過程的在線檢測手段。在AM過程中,孔隙型缺陷是增材制件中最為常見的缺陷之一,多呈現球型或橢球型形貌特征,其尺寸在數十微米至百微米范圍,如圖2所示。孔隙型缺陷對增材制件的拉伸強度、延展性以及疲勞強度等材料力學性能嚴重影響,其產生原因往往與AM工藝參數密切相關,例如,增材過程中材料冷卻速率較大使得熔融態(tài)的金屬材料中的氣體不能及時從熔池中溢出而滯留在材料內部形成孔隙??紤]到制件內孔隙位置、形狀、尺寸、方向和密度等特征與AM工藝參數密切相關,所以通過優(yōu)化工藝參數(如層厚、能量輸入、構建方向、掃描策略、掃描間距和掃描速率)的方式被視為是減少該類型缺陷的重要手段[8]。
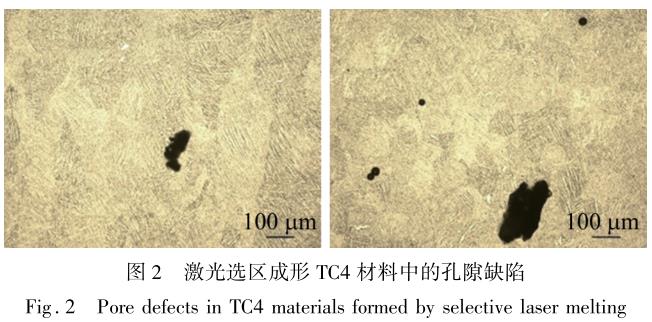
可見,降低AM制件孔隙率的關鍵是如何能夠在增材制造的過程中,對形成異常尺寸的孔隙進行在線檢測,然后反饋給AM制備系統(tǒng)來實時調整工藝參數以降低制件的孔隙率。因此,準確可靠地對AM過程中孔隙缺陷進行無損檢測,對于AM零件質量控制及安全服役均具有重要的科學研究意義和工程應用價值。
圍繞這一問題,國內外學者已經開展了大量探索性研究,試圖從AM制備后的性能檢測、AM零件制備過程中的特征量監(jiān)測和在線式無損檢測技術3個方向,來解決AM零件的質量控制問題[9-12]。
2.1離線式無損檢測技術
離線式無損檢測方式屬于制件加工后檢測,多用于AM結束后對制件的質量評價。實際上,這種方式還可用于建立AM工藝條件和制件質量之間本構關系的研究。例如PARAB等人采用基于同步加速器的X光顯微斷層掃描技術研究了粉末及后處理工藝對孔洞缺陷的影響[9]。由于離線無損檢測無法滿足實時性獲取制件質量信息,無法根據制件狀態(tài)對AM工藝進行的實時調整以及缺陷去除,難以提高AM制件質量及成品率。
2.2基于特征量監(jiān)測的間接式檢測
通過監(jiān)測AM過程能夠反映材料成形等各類不穩(wěn)定現象,據此來預測缺陷的產生,用于實時制造工藝參數的反饋控制。該方式目前主要以熔池尺寸、溫度、光譜以及熔池附近等離子體等作為監(jiān)測參數[10]。例如,CHOO等人利用光電二極管檢測熔池的平均輻射,在確定了熔池參數置信區(qū)間基礎上,對處于在置信區(qū)間外的區(qū)域作為過熱區(qū)域,并據此來判定制件制造質量,研究表明,孔隙缺陷在制件邊緣處出現頻率高于其它區(qū)域[11]??紤]到AM過程中,材料組織演化過程和缺陷產生機制尚未完全明確,而且用于監(jiān)測的過程特征參數與制件缺陷之間的本構關系并不明晰,所以該方法難以保證制件最終質量,需要其它檢測手段進行配合使用。
2.3在線式無損檢測技術
在線式無損檢測方式是AM加工過程急需且有效的一種檢測方式。已經報道的文獻中,AM過程中在線無損檢測技術多集中于X射線技術以及超聲檢測技術,特別是X光計算機層析成像(X-raycomputedtomography,XCT)技術和激光超聲檢測技術,被認為最有潛力應用于AM過程的制件檢測,已經成為本領域的研究熱點[12]。因此,下面將重點介紹XCT技術與激光超聲技術在AM材料檢測方面的主要研究進展。
3、XCT無損檢測技術
倫敦大學學院借助X射線技術的高精度檢測特點,實現了Ti-6242材料在激光AM過程中激光與Ti-6242相互作用過程的連續(xù)觀測,并通過不同時刻孔隙形態(tài)的特征變化分析了其形成機制,如圖3所示[13]。相較于傳統(tǒng)的X射線技術,XCT具有可清晰、準確、直觀地展示制件內部缺陷等優(yōu)點,特別適合于復雜構型的中小型結構件的無損檢測,因此被廣泛用于AM領域中。如諾丁漢大學AM研究團隊采用XCT技術對鋁合金激光選區(qū)熔化AM制件孔隙率進行了檢測,結果表明,該技術可檢測最小孔隙率為0.06%,可檢測出的最小孔隙直徑約為260μm,如圖4所示[14]。
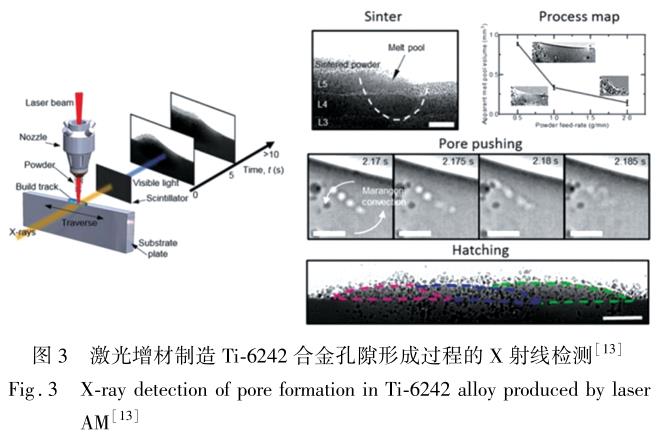
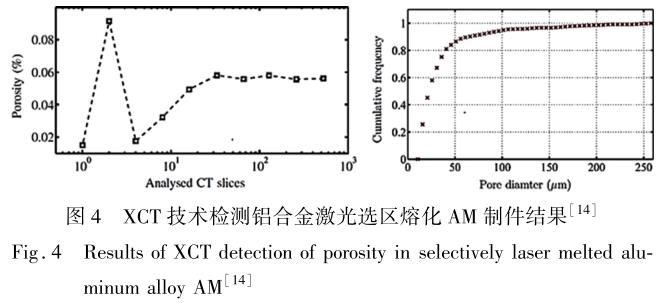
為了進一步提升檢測效率和檢測實時性,研究人員提出了一種AM過程XCT在線無損檢測方式:在制件打印一定層數后進行檢測分析,進而通過逐層打印、固定層數檢測的方式來獲取制件的缺陷信息并用于提高制件的整體質量[15]。圖5所示為Inconel625不銹鋼增材試樣掃描電子顯微鏡(scanningelectronmicro-scope,SEM)及XCT檢測結果。
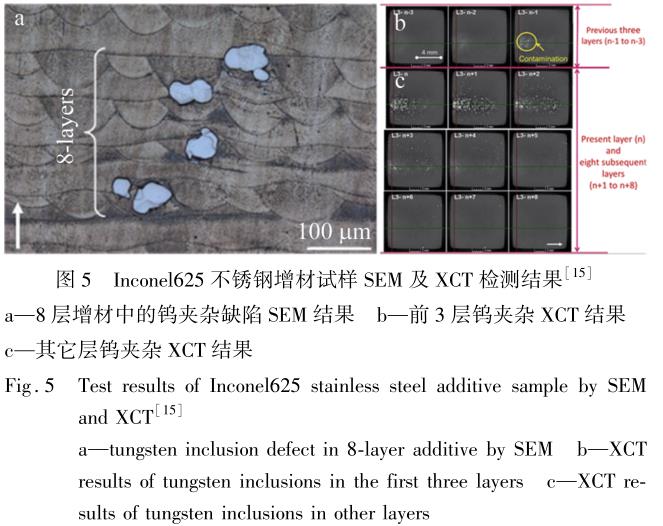
這種方法可實時監(jiān)控成形過程,發(fā)現缺陷后反饋進而修復缺陷,可極大減少制件的廢品率,提高產品的一次性合格率。在線檢測方式對于AM制造零部件質量控制意義更為顯著,已經成為該領域的研究前沿與熱點。
4、激光超聲無損檢測技術
考慮到XCT放射性,目前美國國家航空航天局等機構研究提出了基于超聲檢測技術的AM材料內部孔隙成像的研究思路,主要分為接觸式超聲成像檢測和非接觸式超聲成像檢測兩種方式[16]。在接觸式超聲成像檢測方面,RIEDER等人利用壓電式的脈沖回波超聲法,檢測出了激光增材過程中金屬鋁中直徑約2mm的球型孔隙,進而發(fā)現可以利用超聲波B掃描的檢測方式,監(jiān)測增材過程中激光參數改變誘發(fā)材料中孔隙變化的情況[17]。CHABOT等人利用超聲相控陣技術(10MHz,128陣元)研究在線增材制件中孔隙的可能性時發(fā)現,該方法可以檢測出不小于0.6mm的缺陷,且得到了CT檢測結果的驗證[18]。然而,JAVADI等人最近的研究結果表明,考慮到AM過程中的溫度及制件冷卻速度,一般這種接觸式的超聲相控陣檢測方法需要在制備后36min后實施[19]。因此,接觸式的超聲成像檢測不僅存在檢測滯后的問題,更主要的是無法對缺陷的在線修復和后續(xù)加工工藝進行實時反饋。
在非接觸式超聲成像檢測方面,激光超聲檢測技術因其檢測精度高、適于復雜幾何形狀檢測以及可以遠距離檢測,被認為是最有可能用于AM過程中的主要在線檢測技術之一,近年來備受AM無損檢測研究人員的關注[20-25]。EVERTON等人評估了激光激勵的超聲表面波來檢測AM制件中氣孔缺陷的能力,以鋪粉式激光增材制備的鈦合金試樣中人工孔隙缺陷為研究對象,發(fā)現利用B掃描的方式可以檢測出表面最小直徑為0.725mm的孔隙,該工作沒有評估出內部型氣孔缺陷的檢測能力[20]。LEVESQUE等人研究了一種基于合成孔徑聚焦(syntheticaperturefocusingtech-nique,SAFT)的激光超聲檢測方法,檢測出了激光選區(qū)和電子束兩種增材工藝制備的高溫鎳基合金和鈦合金中內部的未融合和孔隙等缺陷,且檢測結果得到了掃描電鏡檢測結果的驗證[21]。
THEODOSIA等人利用激光機理超聲波并形成超聲相控陣(laserinducedphasedarray,LIPA)的方法檢測出了選區(qū)融化法制備的鋁合金中0.5mm~1.0mm的人工孔隙缺陷,并嘗試用全矩陣捕捉法來對增材過程進行成像式檢測[22],如圖6所示。
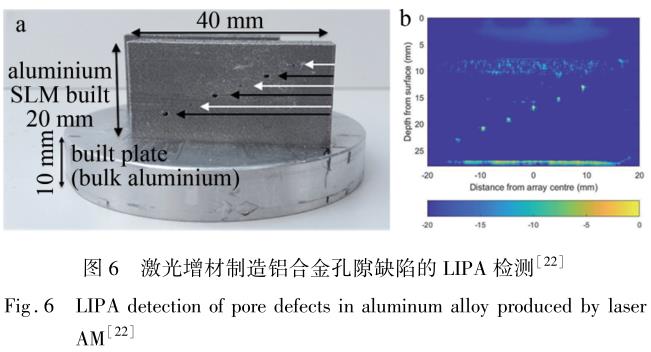
最近,PIERIS等人改進了LIPA方法,利用脈沖重復頻率為5kHz的激光器在熱彈機制下連續(xù)激勵超聲信號,并對信號進行500次的平均,以提高檢測的信噪比,對激光選區(qū)增材工藝制備的鋁鎂合金中6個不同深度下直徑為0.5mm和1.0mm孔隙進行檢測,如圖7所示。結果表明,該方法能發(fā)現其中的5個缺陷[23]。
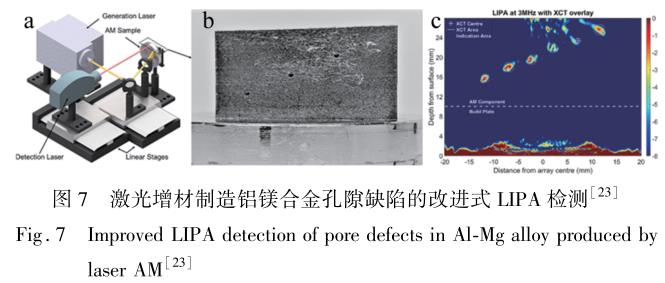
YU等人利用高精度的激光測振儀代替上述研究中的激光干涉儀進行B掃描和C掃描檢測,發(fā)現對于激光增材制造的鈦合金試樣,B掃描和C掃描能夠發(fā)現的最小人工孔隙尺寸分別為0.8mm和0.4mm[24]。
近年來,國內在增材超聲檢測領域也開展了相關跟蹤研究工作。西北工業(yè)大學系統(tǒng)地開展了超聲檢測技術應用于TC4鈦合金激光立體成形制件中缺陷檢測的研究工作,該技術可檢測出的內部人工孔洞類缺陷尺寸約為0.6mm[25]。北京航空航天大學采用超聲C掃描技術對激光AM制造的鈦合金試樣進行了檢測研究,發(fā)現試樣柱狀晶組織誘發(fā)了材料的各向異性和高衰減特性,從而導致C掃描檢測結果受不同深度聲波的能量大小和換能器焦斑的對稱性影響較大,如圖8所示。采用中心頻率10MHz、16陣元的環(huán)形水浸超聲聲速補償成像方式,可以發(fā)現AM鈦合金中直徑為0.8mm、深度為5mm人工平底孔缺陷[26]。
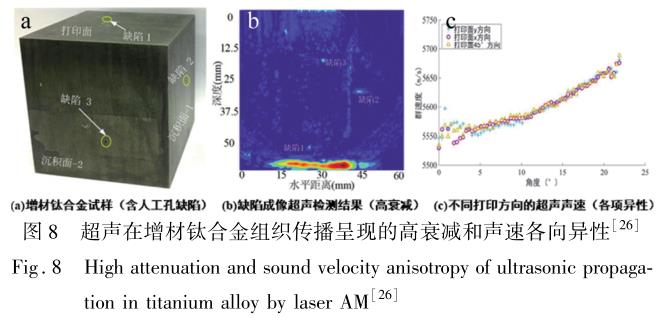
中國航發(fā)北京航空材料研究院采用中心頻率為10MHz的超聲C掃描方式對激光選區(qū)熔化TC4鈦合金中的孔隙進行檢測研究(如圖9所示),結果表明,在超聲波聚焦于鈦合金表面處且檢測靈敏度為0.4mm平底孔當量的條件下,近表面缺陷的超聲C掃描檢測分辨力為3mm、信噪比為16dB,所獲得檢測效果最好[27]。
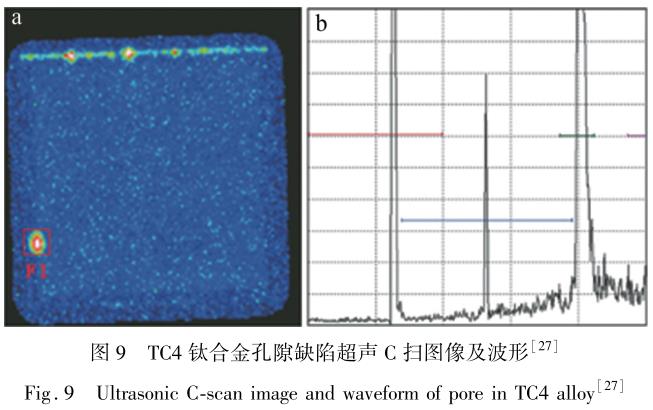
5、結束語
快速有效的無損檢測方法是實現AM制件在航空航天等領域廣泛應用的關鍵技術之一。國內外研究人員在X射線無損檢測和超聲無損檢測研究領域已經取得了技術突破。
(a)通過增材制造過程中材料缺陷的在線無損檢測,包括缺陷檢測、幾何和物理參數測量,將監(jiān)測結果實時反饋給增材制造控制系統(tǒng),進而對加工過程來實時監(jiān)控并調整工藝參數,實現AM制件的控形及控性,是未來確保AM制件質量的主要手段。
(b)增材制造在線無損檢測新技術及裝備的研究對未來生產制造行業(yè)具有深遠影響。AM制件已經呈現大型化、精細化、復雜化發(fā)展態(tài)勢,針對其開展激光超聲、XCT以及TFM超聲相控陣等方法并突破其快速高效的檢測技術,有助于產生AM在線無損檢測新技術及裝備,推動AM制造裝備的升級。
(c)XCT技術在檢測精度和檢測效率方面具有明顯的技術優(yōu)勢,其未來面臨的挑戰(zhàn)主要是被檢測制件的厚度和尺寸對于XCT能量和輻射防護方面的限制。
激光超聲檢測技術具有非接觸、遠距離檢測的優(yōu)點,且可以檢測金屬材料中微米級的孔隙缺陷,初步展示了對于AM材料在線檢測的適用性。AM合金組織特殊性會誘發(fā)復雜的超聲散射噪聲,導致超聲檢測孔隙時存在嚴重的交叉干擾現象,因此給現有超聲檢測方法帶了巨大挑戰(zhàn)。未來超聲檢測技術需要進一步考慮如何降低AM材料組織形貌特殊性對超聲檢測微小孔隙檢測的影響,以確保檢測結果的可靠性與穩(wěn)定性。
參考文獻
[1] WANG Y,ZHOU X F.Research front and trend of specific laser a-dditive manufacturing
techniques[ J].Laser Technology,2021,45(4):475-484(in Chinese).
王勇,周雪峰.激光增材制造研究前沿與發(fā)展趨勢[ J].激光技術,2021,45(4):475-484.
[2] KORNER M E H,LAMBáN M P,ALBAJEZ J A, et al. Systematic literature review:Integration
of additive manufacturing and industry 4. 0[J].Metals,2020,10(8):1061.
[3] HANSEL A,MORI M, FUJISHIMA M,et al. Study on consistently optimum deposition conditions
of typical etal material using additive/subtractive hybrid machine tool [ J]. Procedia Cirp,
2016,46(8):579-582.
[4] WILLIAMS
H,
JONES
E
B.
Additive
manufacturing
standards
for
space
resource
utilization [ J].
Additive
Manufacturing,
2019,
28
(4):676-681.
[5] LI
Z
G,
YIN
Z
M.
The
method
of
the
flaps
of
C919
aircraft
manufac-
turing
quality
control
[J].
Journal
of
Aerospace
Science
and
Techno-
logy,
2020,
8(1):
19-24(in
Chinese).
李紫光,
尹子盟.
大飛機襟翼制造質量控制技術[J].
國際航空
航天科學,
2020,
8(1):
19-24.
[6] KHALIL
M,
TEICHERT
G
H,
ALLEMAN
C,
et
al.
Modeling
strength
and
failure
variability
due
to
porosity
in
additively
manufac-
tured
metals[J]. Computer
Methods
in
Applied
Mechanics
and
Engi-
neering,
2021,373(1):113471-113506.
[7] PANWISAWAS
C,
TANG
Y
B
T,
REED
R
C.
Metal
3D
printing
as
a
disruptive
technology
for
superalloys [ J].
Nature
Communication,
2020,
11(1):
2327-2330.
[8] GORSSE
S,
HUTCHINSON
C,
GOUNé
M,
et
al.
Additive
manufac-
turing
of
metals:
A
brief
review
of
the
characteristic
microstructures
and
properties
of
steels,
Ti-6Al-4V
and
high-entropy
alloys[J].
Sci-
ence
and
Technology
of
Advanced
Materials,
2017,18(1):
584-610.
[9] PARAB
N
D,
ZHAO
C,
ROSS
C,
et
al.
Ultrafast
X-ray
imaging
of
laser-metal
additive
manufacturing
processes[J].
Journal
of
Synchro-
tron
Radiation,
2018,
25(5):
1467-1477.
[10] HONARVAR
F,
VARVANI-FARAHANI
A.
A
Review
of
ultrasonic
testing
applications
in
additive
manufacturing:
Defect
evaluation,
material
characterization,
and
process
control [ J ].
Ultrasonics,
2020,
108(9):106227.
[11] CHOO
H,
SHAM
K
L,
BOHLING
J,
et
al.
Effect
of
laser
power
on
defect,
texture,
and
microstructure
of
a
laser
powder
bed
fusion
pro-
cessed
316L
stainless
steel [ J].
Materials
&
Design,
2019,
164
(4):
107534.
[12] MILLON
C,
VANHOYE
A,
OBATON
A
F,
et
al.
Development
of
laser
ultrasonics
inspection
for
online
monitoring
of
additive
manufac-
turing[J].
Welding
in
the
World,
2018,
62(3):
653-661.
[13] CHEN
Y
H,
CLARK
S
J,
SINCLAIR
L,
et
al.
Synchrotron
X-ray
imaging
of
directed
energy
deposition
additive
manufacturing
of
tita-nium
alloy
Ti-6242[ J].
Additive
Manufacturing,
2021,
41 ( 5):
101969.
[14] MASKERY
I,
ABOULKHAIR
N
T,
CORFIELD
M
R,
et
al.
Quan-
tification
and
characterisation
of
porosity
in
selectively
laser
melted
Al-Si10-Mg
using
X-ray
computed
tomography[ J].
Materials
Cha-
racterization,
2016,
111(1):
193-204.
[15] MOHAMMAD
M,
REZA
Y,
RAO
P,
et
al.
In-process
monitoring
of
material
cross-contamination
defects
in
laser
powder
bed
fusion[J].
Journal
of
Manufacturing
Science
&
Engineering,
2018,
140(11):
111001.
[16] WALLER
J,
SAULSBERRY
R,
PARKER
B,
et
al.
Summary
of
NDE
of
additive
manufacturing
efforts
in
NASA
[ J].
AIP
Confe-
rence
Proceedings,
2015,
1650(1):
51-62. [17] RIEDER
H,
SPIES
M,
BAMBERG
J,
et
al.
On-
and
offline
ultra-
sonic
characterization
of
components
built
by
SLM
additive
manufac-
turing[J].
AIP
Conference
Proceedings,
2016,1706(1):130002.
[18] CHABOT
A,
LAROCHE
N,
CARCREFF
E,
et
al.
Towards
defect
monitoring
for
metallic
additive
manufacturing
components
using
phased
array
ultrasonic
testing[J].
Journal
of
Intelligent
Manufactur-
ing,
2020,
31(5):1191-1201.
[19] JAVADI
Y,
MOHSENI
E,
MACLEOD
C
N,
et
al.
Continuous
mo-
nitoring
of
an
intentionally-manufactured
crack
using
an
automated
welding
and
in-process
inspection
system[ J].
Materials
&
Design,
2020,191(7):108655.
[20] EVERTON
S,
DICKENS
P,
TUCK
C,
et
al.
Evaluation
of
laser
ul-
trasonic
testing
for
inspection
of
metal
additive
manufacturing[ J].
Proceedings
of
the
SPIE,
2015,9353:
935316.
[21] LEVESQUE
D,
BESECOND
C,
LORD
M,
et
al.
Inspection
of
addi-
tive
manufactured
parts
using
laser
ultrasonics[ J].
AIP
Conference
Proceedings,
2016,
1706(1):
130003.
[22]
THEODOSIA
S,
YASHAR
J,
WILLIAM
K,
et
al.
Laser
induced
phased
arrays
for
remote
ultrasonic
imaging
of
additive
manufactured
components[C] / / 57th
Annual
Conference
of
the
British
Institute
of
Non-Destructive
Testing.
Northampton,
UK:
BINDT,
2018:
174-
182.
[23]
PIERIS
D,
STRATOUDAKI
T,
JAVADI
Y,
et
al.
Laser
induced
phased
arrays
(LIPA)
to
detect
nested
features
in
additively
manu-
factured
components [ J].
Materials
&
Design,
2020,
187 ( 3):
108412.
[24] YU
J,
ZHANG
D
Q,
LI
H,
et
al.
Detection
of
internal
holes
in
ad-
ditive
manufactured
Ti-6Al-4V
part
using
laser
ultrasonic testing
[J].
Applied
Sciences,
2020,
10(1):365-376.
[25] RUAN X Q,LIN X,HUANG Ch P,et al.Effect of microstructure of laser solid forming TC4 titanium alloy on ultrasonic parameters[J].Chinese Journal of Lasers,2015,42(1):0103005(in Chin-ese).
阮雪茜,林鑫,黃春平,等.TC4激光立體成形顯微組織對超聲參量的影響[J].中國激光,2015,42(1):0103005.
[26] LI W T,ZHOU Zh G.Research on ultrasonic array testing methods of laser additive-manufacturing titanium alloy[ J].Journal of Me-chanical Engineering,2020,56(8):141-147(in Chinese).
李文濤,周正干.激光增材制造鈦合金構件的陣列超聲檢測方法研究[J]. 機械工程學報,2020,56(8):141-147.
[27] LIN L Zh,YANG P H,HAN B,et al.Ultrasonic testing of Ti-6Al-4V titanium alloy material
manufacured by selective laser melting [J].Nondestructive Testing,2021,43(6):12-15(inChinese).
林立志,楊平華,韓波,等.激光選區(qū)熔化增材制造 Ti-6Al-4V鈦合金的超聲檢測[J]. 無損檢測,2021,43(6):12-15.
無相關信息