1、引言
將激光增材制造技術用于鈦合金的成形,能夠降低復雜結構鈦合金的加工成本,具有重要的工程價值[1-3],鈦合金激光增材制造也被業(yè)內認為是增材制造領域最具挑戰(zhàn)性的前沿發(fā)展方向之一,并且存在不同方面的研究熱點和難點[4-8]。鈦合金激光增材制造可分為激光粉末選區(qū)成形和激光同步材料送進成形兩大類,按照成形機理又可細分為鈦合金選區(qū)激光熔化、鈦合金激光送粉沉積和鈦合金激光送絲沉積三種技術。基于合金粉末的前兩種增材制造技術成形精度高,適合加工形狀復雜的小型構件,但材料利用率低,而且粉末對環(huán)境有一定污染,同時存在操作環(huán)境要求較高等諸多問題[9,10]。相較而言,基于合金絲材的激光送絲沉積(Wire-feedingLaserMetalDeposition,WLMD)增材制造技術的材料利用率很高且污染較少,更加經(jīng)濟實用,從而適合大尺寸構件的高效加工[11]。尤其是對于未來爭相布局的太空金屬增材制造而言,激光送絲設備結構相對簡單,絲材更易存儲運輸,并且激光送絲能夠克服太空微重力環(huán)境的影響[12,13]。因此,推動WLMD技術的進一步發(fā)展具有重要應用價值和前瞻意義。
選區(qū)激光熔化和激光送粉沉積發(fā)展較早,相關研究報道較多,屬于較為成熟的鈦合金增材制造技術[14,15]。激光送絲沉積則屬于正在發(fā)展的增材技術,其工程化應用還需工藝的持續(xù)優(yōu)化和完善,故具有較大的研究空間。目前,鈦合金WLMD的研究主要集中在基礎成形工藝方面,其技術工藝還存在許多不足,缺少對于組織性能的評價,并且缺乏較為系統(tǒng)的概括性進展總結。因此,本文綜述現(xiàn)階段鈦合金WLMD技術的基本原理和工藝分類,討論WLMD關鍵工藝參數(shù)、所成形鈦合金的組織性能以及調控方法的研究進展,并展望WLMD增材制造技術未來研究目標與發(fā)展趨勢,以便為該技術后續(xù)研究提供參考,促進其在更多領域的廣泛應用。
2、激光送絲沉積技術成形原理
WLMD以金屬絲材為原材料,采用激光為熱源熔化絲材并按規(guī)劃路徑進行生產(chǎn)加工,耗時短且靈活性好。圖1(a)是典型WLMD成形裝置示意圖,成形裝置主要包括激光系統(tǒng)、控制系統(tǒng)、沉積平臺、保護氣系統(tǒng)、送絲機構以及機械臂幾大部分。開始打印時,在控制系統(tǒng)命令下,保護氣系統(tǒng)先行啟動,為沉積過程提供真空氣氛。在送絲系統(tǒng)啟動的同時,激光系統(tǒng)發(fā)射激光將送絲嘴中出來的金屬絲熔化,金屬絲材持續(xù)送入熔池中,實現(xiàn)熔化-凝固的過程,同時機械臂按照預先設定的路徑移動,在金屬基板上形成沉積層。如此不斷循環(huán),最終實現(xiàn)三維立體零件的制造[16-18]按照送絲方式的不同,WLMD技術可以分為旁軸送絲和同軸送絲兩種[19-21]。WLMD旁軸送絲,即金屬絲從激光束外通過送絲機構輸送到激光束的焦點上進行熔化,其平臺搭建相對容易。然而,由于熔覆過程受到送絲方向性的限制,會影響沉積過程中沉積頭的運動的自由度,同時沉積過程具有明顯的方向性,所成形的沉積層尺寸和性能一致性較差,并且對光絲的相對位置的耦合性要求較高,如圖1(b)所示[20]。WLMD同軸送絲的絲材由激光中心送入,雖然可以有效避免送絲方向性問題,但其重點主要在于激光焊槍的設計和制造難度大,這是因為焊槍上集成了光路、氣路、送絲和冷卻等多種功能,如圖1(c)所示[21],目前該技術正處于實驗室到市場化的拓展階段,因而屬于較新型的增材制造技術。
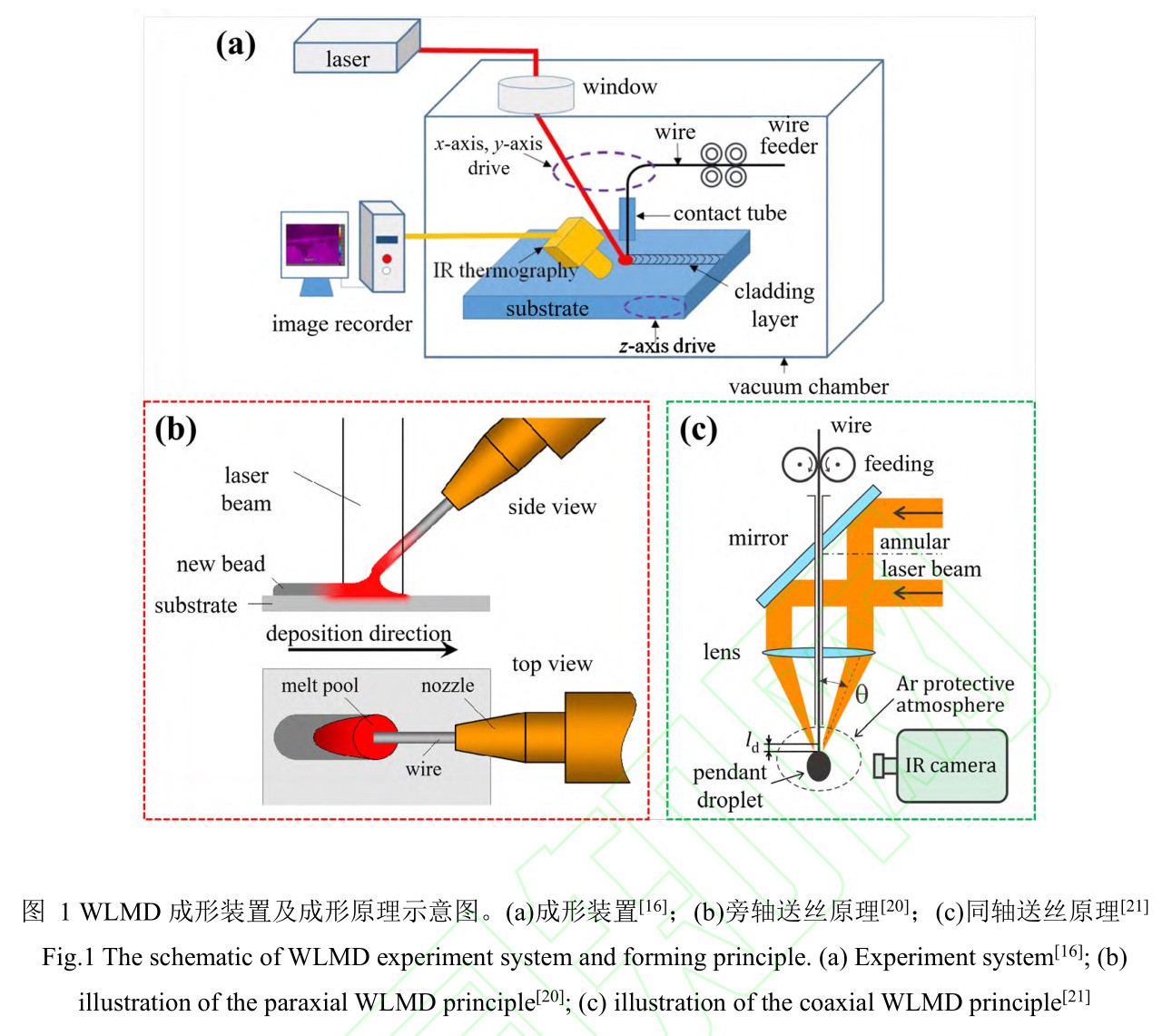
3、激光送絲沉積技術及調控
3.1旁軸送絲技術
激光送絲增材制造技術基于激光填絲焊接技術發(fā)展而來,因此,旁軸送絲技術一直是WLMD領域的主要研究方向[22]。WLMD旁軸送絲工藝涉及許多參數(shù)的變化,這些工藝參數(shù)的改變會對沉積過程有一定的影響。Mok等[23,24]較早采用半導體激光器送絲制備了TC4鈦合金,發(fā)現(xiàn)絲材進入熔池的方向和角度等都會影響沉積層的表面光潔度、沉積精度及顯微組織,沉積過程的掃描速度、激光功率和送絲速度也會對沉積層組織產(chǎn)生影響,并導致成形件的力學性能發(fā)生變化。
送絲方向對WLMD旁軸送絲成形效果影響顯著,相對于沉積方向會產(chǎn)生前送絲、側送絲和后送絲三種方向,原理如圖2(a)、(b)和(c)所示[25]。前送絲方式是絲材從熔池前方送入熔池進行熔化,熔化后的金屬液進入后方的熔池,后送絲方式與之相反,側送絲方向則介于前送絲與后送絲之間。Kim等[26]認為前送絲方式下,即使送絲速度和位置公差很大,絲材也能完全熔化。同樣地,Syed等[27]的研究也表明前送絲比后送絲對送絲速度和位置具有更好的適應性,在前送絲時絲材被熔池散發(fā)的熱量熔化,對熔池的擾動較小并且絲材反射激光較少,因而熔池表面光潔度較好,沉積層內部致密且缺陷較少,而后送絲方式則帶來較多的缺陷。此外,Yang等[28]分析認為在前送絲時絲材不會阻擋激光作用在基板上,基板可以獲得最大的熱輸入,并且熔滴在較高溫度基板上的潤濕度也能提高,從而獲得良好的表面質量。
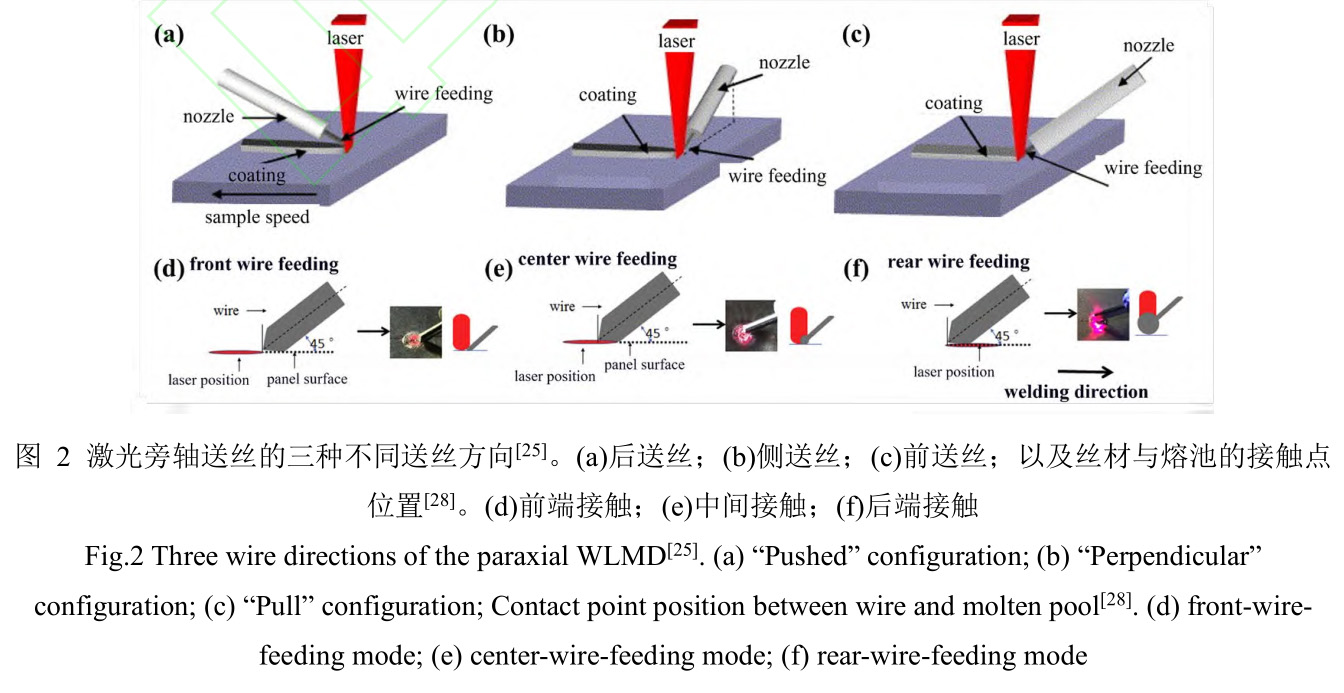
Sun等[29]和Shen等[30]的研究也發(fā)現(xiàn)當送絲位置在熔池的前方時成形質量較高。與此同時,絲材對激光的阻擋會使得熔池受熱不均勻,所以當絲材接觸點位于熔池前端時能夠獲得較好的沉積效果,如圖2(d)所示[28]。
不同的送絲角度和位置也會產(chǎn)生不同的影響。Moures等[25]和Mok等[24]研究結果表明,將工藝定為前送絲和45°角度時,能夠得到最高的沉積速率,并且試樣表面光滑質量較好。
Mortello等[31]發(fā)現(xiàn),當絲材高于熔池時,熔化的金屬液滴落入熔池時會使沉積層表面出現(xiàn)波紋,從而降低沉積層表面質量;但是當絲材與熔池相接觸時,由于金屬熔液傳遞模式由重力驅動變?yōu)楸砻鎻埩︱寗樱练e工藝效果也更加穩(wěn)定。
盡管現(xiàn)在國內外的研究主要集中在旁軸送絲方案上,但是仍然存在幾點明顯的不足之處,比如金屬絲材和激光束的位置要求高并且耦合性差,復雜零件成形時沉積頭的自由度會受到限制,以及會產(chǎn)生送絲方向性等問題。旁軸送絲方案想要保持前送絲沉積就需要送絲噴嘴圍繞熔覆頭快速旋轉調整方向,或者通過旋轉基體達到保持前送絲的效果。實際上,要解決旁軸送絲方向問題,就會增加機械設計與控制的難度,而且調整方向需要更多的時間,也會帶來移動軌跡拐角處材料過渡堆積等問題[32]。
3.2同軸送絲技術
WLMD同軸送絲技術不存在送絲方向的問題,在拐角等方向急劇變化的特殊位置,僅需簡單地通過X和Y軸的加速和減速就能實現(xiàn)過渡,并且不會使得材料過渡堆積,可以極
大地簡化機械結構與電氣控制。目前主流的激光同軸送絲技術可以根據(jù)分光的原理分為三種[33],即分三光束光內同軸技術、多光束集成光內同軸技術和分環(huán)形光束光內同軸技術,其原理和熱源分布如圖3所示。德國FraunhoferILT研究所先后利用分三光束和分環(huán)形光束光內同軸技術制造了WLMD沉積設備,并聯(lián)合Precitec公司推出了商用版分環(huán)形WLMD同軸送絲沉積設備;而在國內,蘇州大學利用分三光束光內同軸技術原理、重慶綠色智能技術研究所團隊利用多光束集成光內同軸技術原理分別研發(fā)了用于實驗室研究的WLMD同軸送絲沉積設備[16,34,35]。
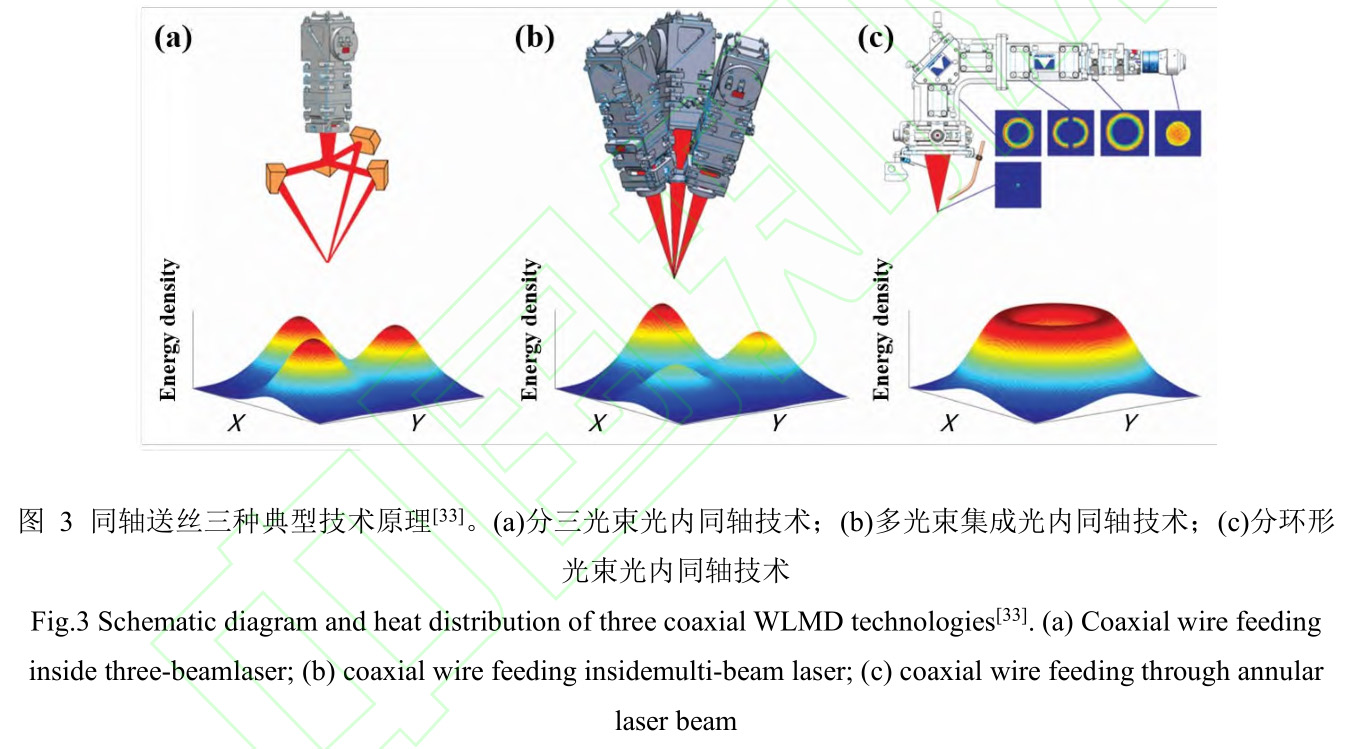
由于同軸送絲工藝的特殊性,同軸送絲技術的離焦量工藝窗口較窄[36]。Ji等[37]發(fā)現(xiàn)當離焦量在-1.5~-2.5mm的范圍內時才能形成光滑連續(xù)的熔道。當離焦量過大時,環(huán)形激光光斑孔徑過大,不足以充分熔化絲材,會形成鋸齒狀熔道;而當離焦量過小時,環(huán)形激光光斑孔徑過小,激光能量集中到絲材上,會使得絲材迅速熔化成熔滴并持續(xù)長大,最終形成不連續(xù)的滴狀熔道。為了更好地分析熔道形狀與送絲工藝參數(shù)的關系,引入了寬高比和稀釋率這兩個關鍵指標來評價熔道質量[38]。通常,掃描速度增大,熔道的寬度減小,而熔道的高度明顯下降,使得寬高比增大;激光功率增大,激光光斑的能量密度也增大,熔道的寬度和深度也隨之增大,使得熔道的稀釋率增大[34]。相對來說,送絲速度對熔道的高度影響更顯著,送絲速度的增加能夠提高金屬絲材的供給量,使得熔高顯著增加[16]。為了更好地理解激光功率的影響,圖4提出了一種預測同軸送絲工藝激光功率密度的模型[39],可模擬打印過程中任何表面上任意數(shù)量的光束和功率密度,并且能預測各種工藝參數(shù)下激光光斑的形狀和大小,從而有助于優(yōu)化打印軌跡和制造策略。
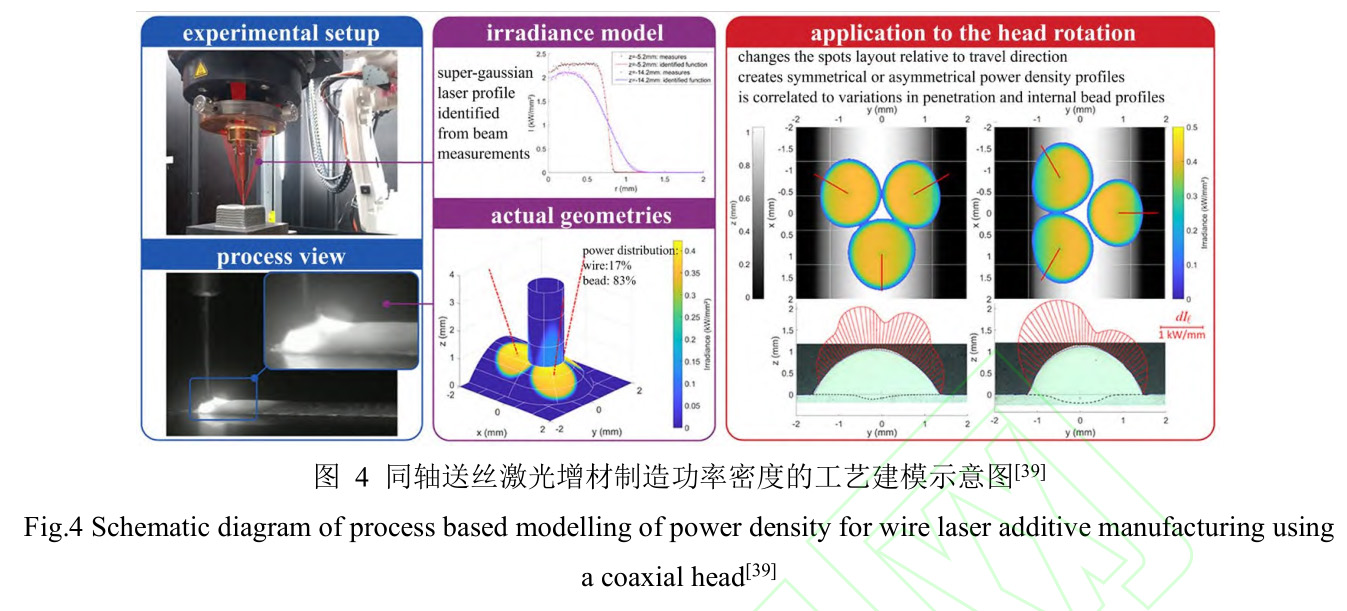
針對鈦合金的WLMD同軸送絲打印,德國的FraunhoferILT研究所、勃蘭登堡工業(yè)大學和西班牙工業(yè)研究中心等先后對TC4合金進行了探索[40-42],成功實現(xiàn)了鈦合金典型結構的增材制造。Kelbassa等[40]利用連續(xù)環(huán)形激光束開展同軸送絲WLMD試驗,將惰性氣體通過同軸方式輸送,避免熔池暴露在空氣中發(fā)生氧化,如圖5所示。這種設計同時能夠減少沉積頭的集成質量,使得沉積頭具有高動態(tài)的特征,加上纖細的Ti-6Al-4V絲材原料,可以近凈成形復雜的幾何形狀。中國船舶七二五所和上海產(chǎn)業(yè)技術研究院分別利用Precitec分環(huán)形激光同軸送絲沉積設備對鈦合金零部件增材制造工藝進行探索[43],其中對直徑1.0~1.6mm鈦合金絲材研究表明,當激光器功率為3000W,熔敷效率可達5~30g/min。而Du等[44]研究了真空條件對WLMD同軸送絲制造Ti-6Al-4V薄壁件的作用,發(fā)現(xiàn)沉積過程中的高度增量應在適當范圍內,并與層高相匹配;當層間冷卻時間為1s時,熱積累量較大,在高激光功率、層間冷卻時間大于5s的條件下,薄壁件層寬更容易保持一致性。
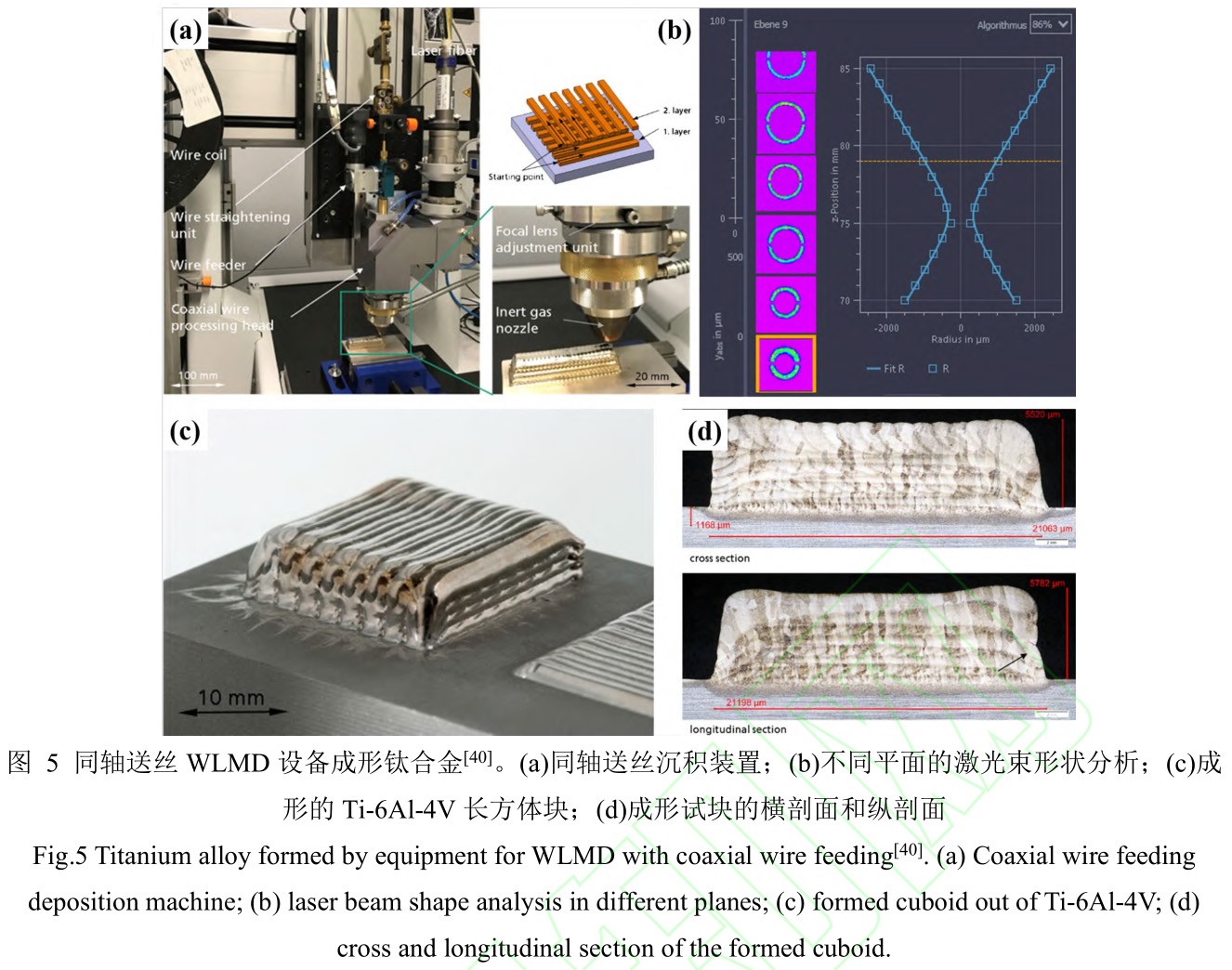
盡管同軸送絲方案具有諸多優(yōu)點,但是當前對于WLMD同軸送絲技術的研究總體仍然較少,其難點主要在于光路的轉換難度較高,比如,將實心光束轉換為分環(huán)形光束,同時金屬絲要避開環(huán)形光束并從中心送進,完成這一過程需要考慮不同光路、匯聚角度、光斑內外徑等對絲材的影響。此外,采用該方案時激光功率與送絲速度的匹配要求會更高,否則容易出現(xiàn)絲材與熔池底部相撞使得絲材彎曲,使熔池不穩(wěn)定,從而影響成形質量。
4、激光送絲沉積鈦合金組織、性能及調控
4.1激光送絲沉積鈦合金的組織特征
盡管WLMD在成形工藝方面具有特殊優(yōu)勢,但沉積的試樣普遍存在氣孔、未熔合、應力和組織性能不均勻等問題[45]。因此,成形樣品的組織演變機理和性能調控方法仍然是WLMD技術近年來的研究重點。由于激光熔化沉積時熔池內部熱質傳輸過程較為復雜,因此對沉積過程中鈦合金顯微組織的演變行為開展研究,將有利于建立WLMD鈦合金的組織和性能映射關系。
研究者們[46-48]發(fā)現(xiàn)WLMD成形樣品的組織形貌具有很大的相似性,其沉積層通常為柱狀晶,頂部為等軸晶。沉積過程類似于鑄造當中的定向凝固,熔池底部由于較大的溫度梯度的作用,會在前一層的基礎上發(fā)生外延生長,從而形成穿過兩個或者多個沉積層的柱狀晶,而在熔池頂部會形成等軸晶,這是由于頂部與空氣接觸從而能較快冷卻。相似地,鈦合金的增材制造組織中常見問題是,沿著試樣沉積的方向,會生成粗大的初生β柱狀晶粒,對于WLMD鈦合金而言,β柱狀晶粒長度能達到幾百微米或幾個毫米[49]。此外,晶界的兩側存在密集排列的針片狀α相,一般是由晶界處形核并向晶內生長而成,由于晶界α相在橫向載荷作用下會使得材料過早斷裂,從而顯著地影響成形件的塑性變形行為[50]。也就是說,鈦合金熔池內部存在的明顯溫度梯度,使得初生β柱狀晶粒沿溫度梯度方向的定向生長通常會形成較強的<001>織構,并產(chǎn)生α轉變織構,從而對疲勞性能產(chǎn)生不利影響,同時使得力學性能出現(xiàn)各向異性[51]。
對于工業(yè)上應用最多的(α+β)型鈦合金,其組織演變過程一般如下[52]:沉積層凝固時,內部首先發(fā)生液相→β相的相變。隨著溫度持續(xù)降低,β相穩(wěn)定元素擴散系數(shù)較大而使得原始β晶粒不斷長大,并將晶內的α相穩(wěn)定元素持續(xù)排到晶界處。一旦溫度降低至α+β兩相區(qū)時,將發(fā)生β→α轉變。由于β晶界處富集了α相穩(wěn)定元素,導致α相在β相晶界上形核,并沿晶界形成連續(xù)的α相層,即晶界α相。當冷卻速率較慢時,晶界α相會逐漸在β晶粒內部形成平行的片狀α相,并與其它的片狀α相交織從而停止進一步生長。如圖6所示為(α+β)鈦合金冷卻時的相變化曲線以及WLMD鈦合金典型組織形貌,合金在冷卻速度較高時內部基本為馬氏體結構,但隨著冷卻速度降低到410℃/s以下時,魏氏體會逐漸代替馬氏體結構[46,53,54]。
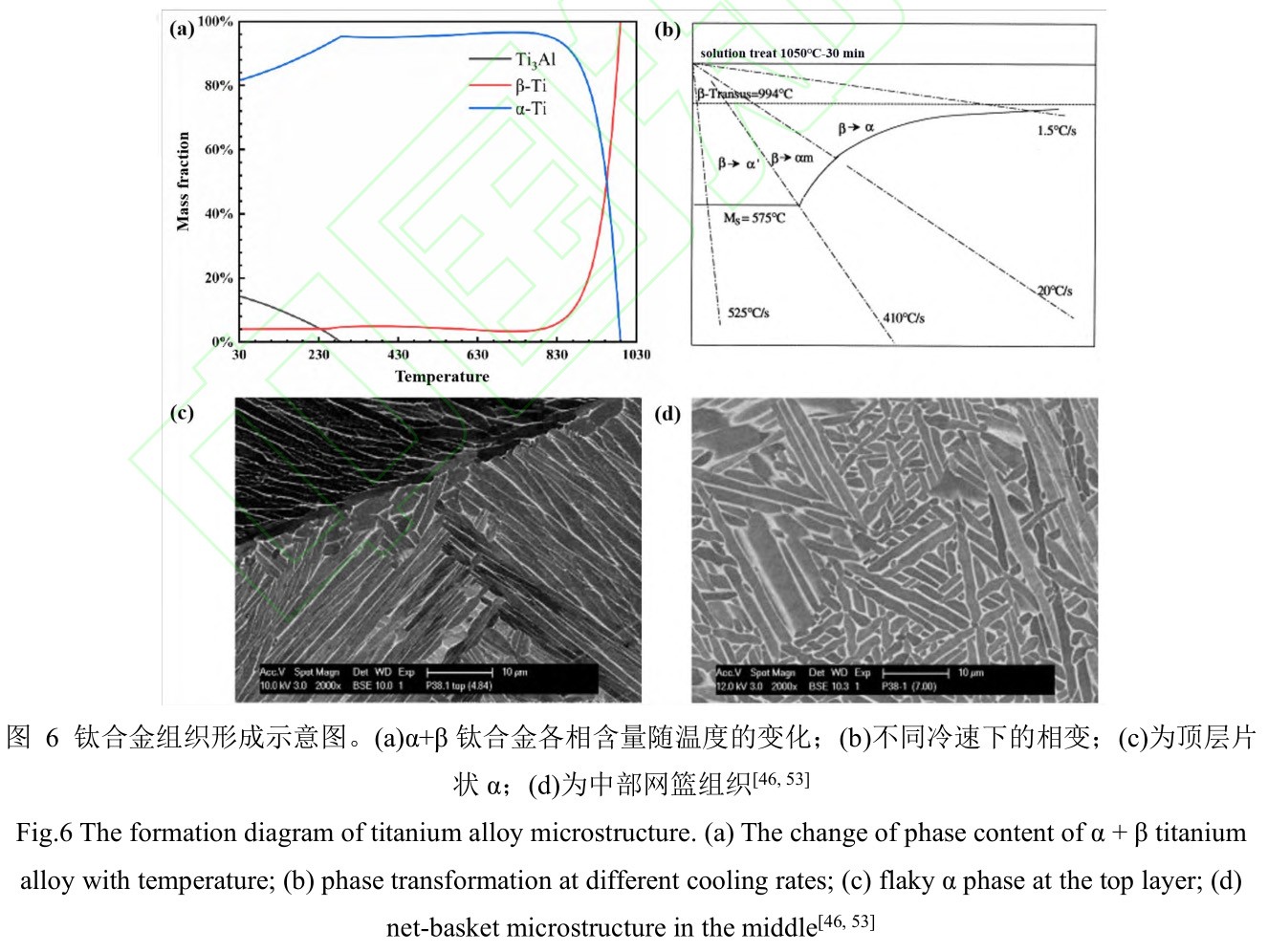
簡言之,WLMD試樣內部通常由粗大的β柱狀晶、晶界α相、晶內片層狀α集束以及少量馬氏體相組成??紤]到魏氏組織和馬氏體力學性能較差,WLMD鈦合金理想的組織為較小尺寸的初生β晶粒,以及盡可能多的α集束和網(wǎng)籃組織[55]。然而,不同的復合工藝和環(huán)境會對WLMD組織產(chǎn)生影響。Guo等[56]將電弧和激光增材制造進行復合時,所成形的TC11鈦合金在沉積狀態(tài)下微觀組織主要是由層狀α團簇組成的魏氏組織。固溶時效處理后,組織轉變?yōu)闂l形α、β相和細針狀馬氏體相組成的網(wǎng)籃形態(tài),水淬后形成大量的αs次生相和α′馬氏體相,與此同時,α相和β相的尺寸會由于空冷而變粗大。而Guo等[57]采用如圖7所示的水下WLMD技術,通過增加保護氣體流量到80L/min,同時熱輸入從1.75kJ/cm提高到2.5kJ/cm,獲得了均勻無氧化的水下熔覆層;隨著熱輸入量的增加,α板條的晶粒尺寸和厚度增加,α′的含量減少,氧化現(xiàn)象也有所改善,但柱狀β晶粒和球形β晶粒尺寸均增大。不同熱輸入層的顯微組織由不同尺寸的片層α相和針狀α′相組成。此外,冷卻速率的降低抑制了針狀馬氏體的單向生長,使馬氏體的排列接近無序狀態(tài),熔覆層的變形更加均勻,有效地防止了裂紋的擴展。
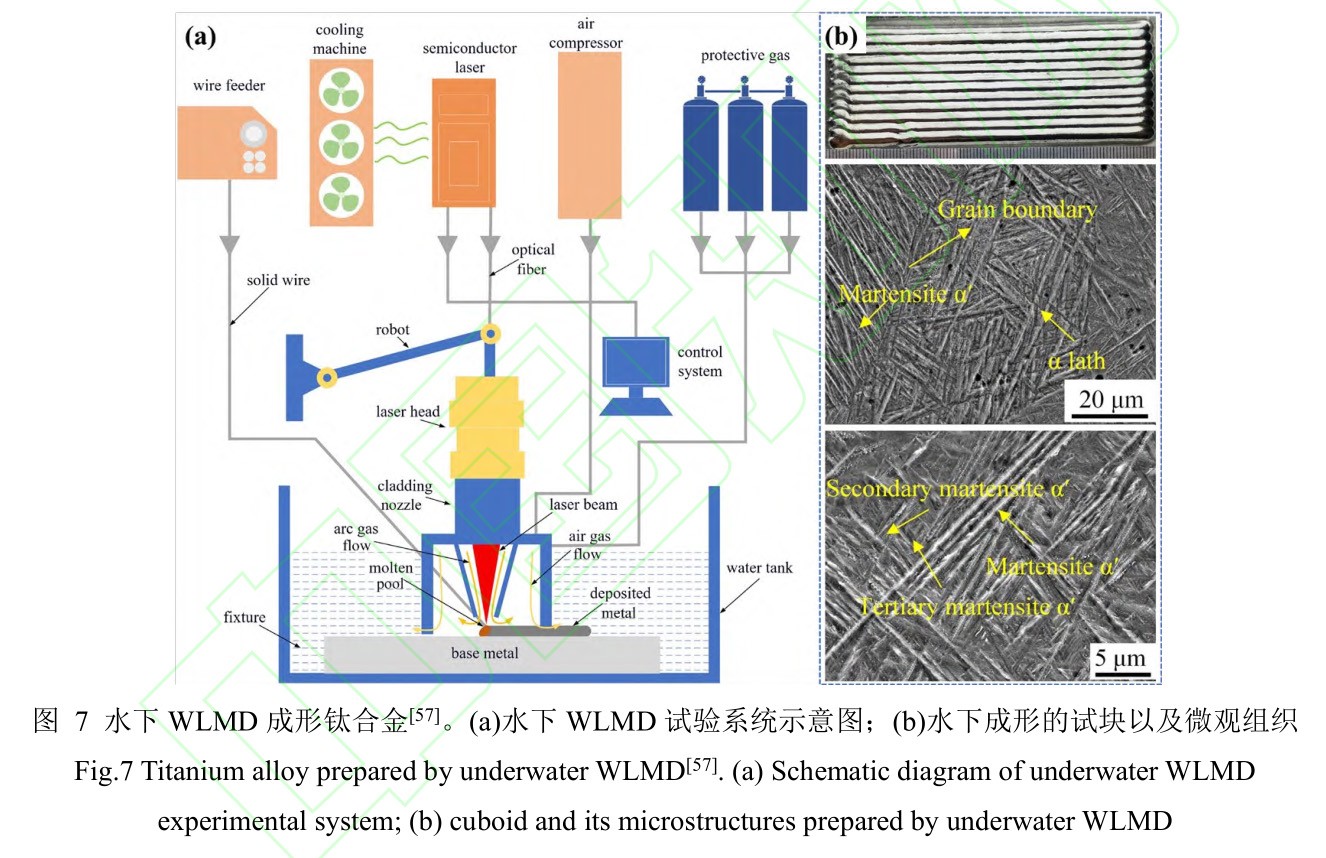
4.2激光送絲沉積鈦合金的性能及調控
由于WLMD鈦合金內部組織分布不均而使各個位置力學性能出現(xiàn)差異。通常試樣硬度受沉積工藝參數(shù)的影響較小,而拉伸性能則在垂直和平行基板的方向上表現(xiàn)出較大差別,主要在于垂直方向的延伸率優(yōu)于平行方向。這是因為平行方向有著更多的β柱狀晶界,晶界處的α相在載荷作用下會提前失效。沉積工藝參數(shù)會對熔池熱輸入產(chǎn)生重要影響,進而形成不同的組織形貌,并對沉積試樣的性能產(chǎn)生關鍵作用。因此,利用沉積過程中以及沉積完成后的各種工藝手段對組織進行優(yōu)化,有助于獲得較好性能的合金,對此已有大量組織性能調控相關的研究[58]。表1為不同成形技術所制備鈦合金力學性能的對比,可見,送絲增材制造鈦合金構件的力學性能受控于工藝,因而高性能構件的增材制造需要建立材料-工藝-組織-性能的一體化設計、制造與調控理論及方法。

激光增材制造成形過程中繁雜的熱循環(huán)以及殘余應力分布,會在沉積層中產(chǎn)生較為嚴重的變形甚至開裂,從而對性能產(chǎn)生關鍵的影響,而數(shù)值模擬是解決該類問題的有力工具。任朝暉等[63]對鈦合金WLMD過程中的溫度場和應力場開展了模擬研究,采用ABAQUS軟件建立完全熱力耦合的有限元模型,研究了Ti-6Al-4V單道多層沉積件的熱循環(huán)特性和應力分布,如圖8所示,發(fā)現(xiàn)隨著沉積層數(shù)的增加,熱累積效應逐漸變強,且冷卻速率下降;薄壁沉積件整體的殘余應力為拉應力狀態(tài),x方向明顯大于另外兩個方向,然而垂直于掃描方向較易產(chǎn)生裂紋等缺陷;同時,中部殘余應力相對穩(wěn)定,最大殘余應力集中在沉積層兩端與基板交界處。
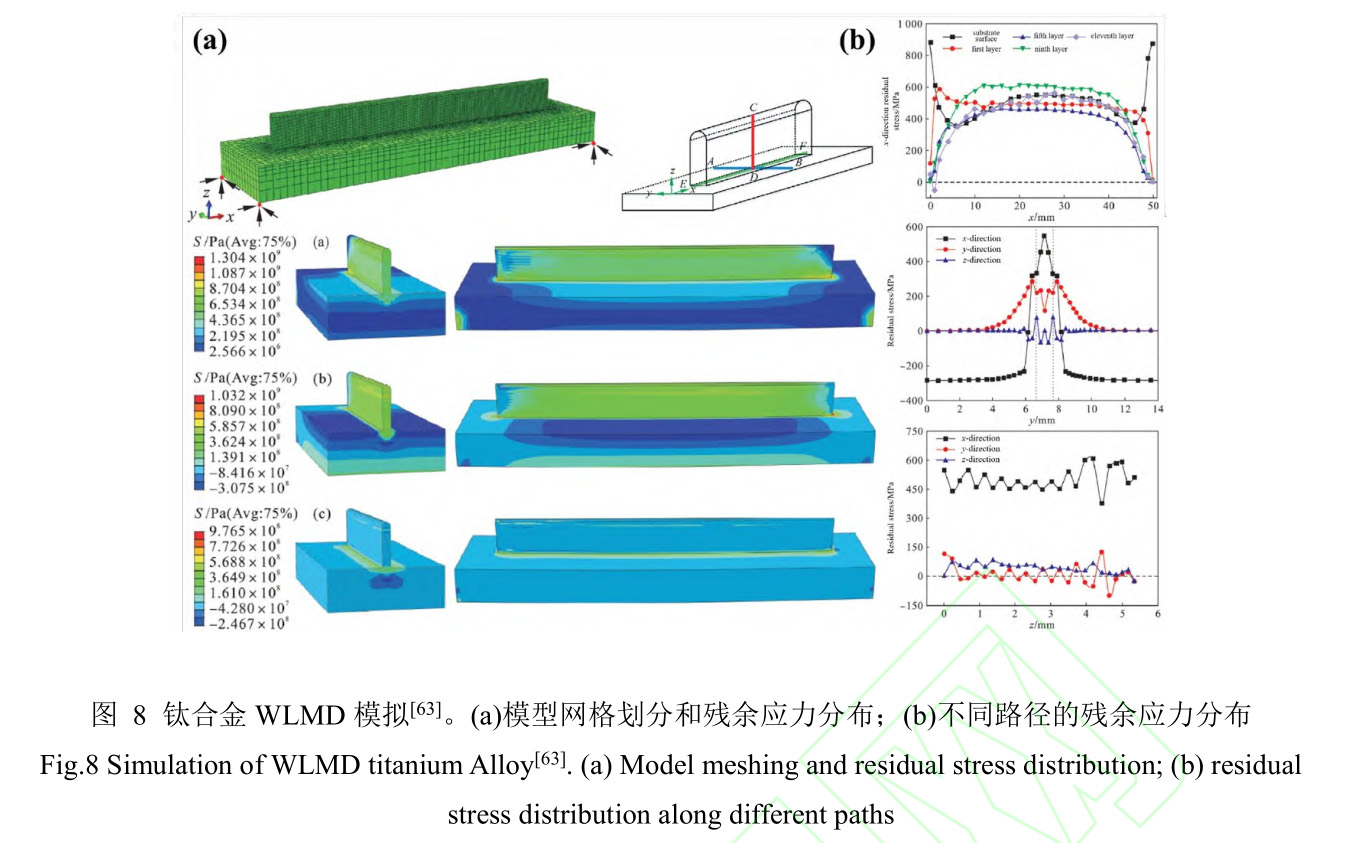
為了進一步調控組織性能,Ye等[64]利用超聲微鍛造對WLMD鈦合金進行研究,結果表明,振幅和鍛造力會使得Ti-6Al-4V試樣中出現(xiàn)大量等軸β晶粒,其形態(tài)也可以通過工藝參數(shù)進行控制,如圖9所示,隨著振幅的增大,等軸β晶粒平均尺寸減??;隨著鍛造力的增加,沉積層與基板界面處的缺陷數(shù)量增加,但顯微硬度也隨之增大。Yang等[65]研究了超聲沖擊前后成形樣品的變化,發(fā)現(xiàn)超聲沖擊后的樣品殘余應力遠低于沉積態(tài)樣品,同時提高了拉伸強度,但伸長率有所降低。Donoghue等[66]將軋制與沉積進行工藝復合,發(fā)現(xiàn)每一層沉積后只需較低的變形量就能顯著地減小晶粒尺寸,并且β和α相織構也大幅降低到接近隨機分布,同時這些破碎晶??梢栽诤笠粚映练e過程中再次加熱時作為再結晶晶核。Sabban等[67]通過在接近但低于β轉變溫度的條件下循環(huán)熱處理TC4鈦合金,使得針片狀α相逐漸轉變?yōu)榍驙?,球形化雙相組織將沉積試樣的延展性提高了80%,韌性提高了66%。除此之外,還有固溶時效熱處理[68,69]、電脈沖熱處理[70]和等通道角擠壓[71]等方式來改善合金組織,從而對力學性能進行調控。
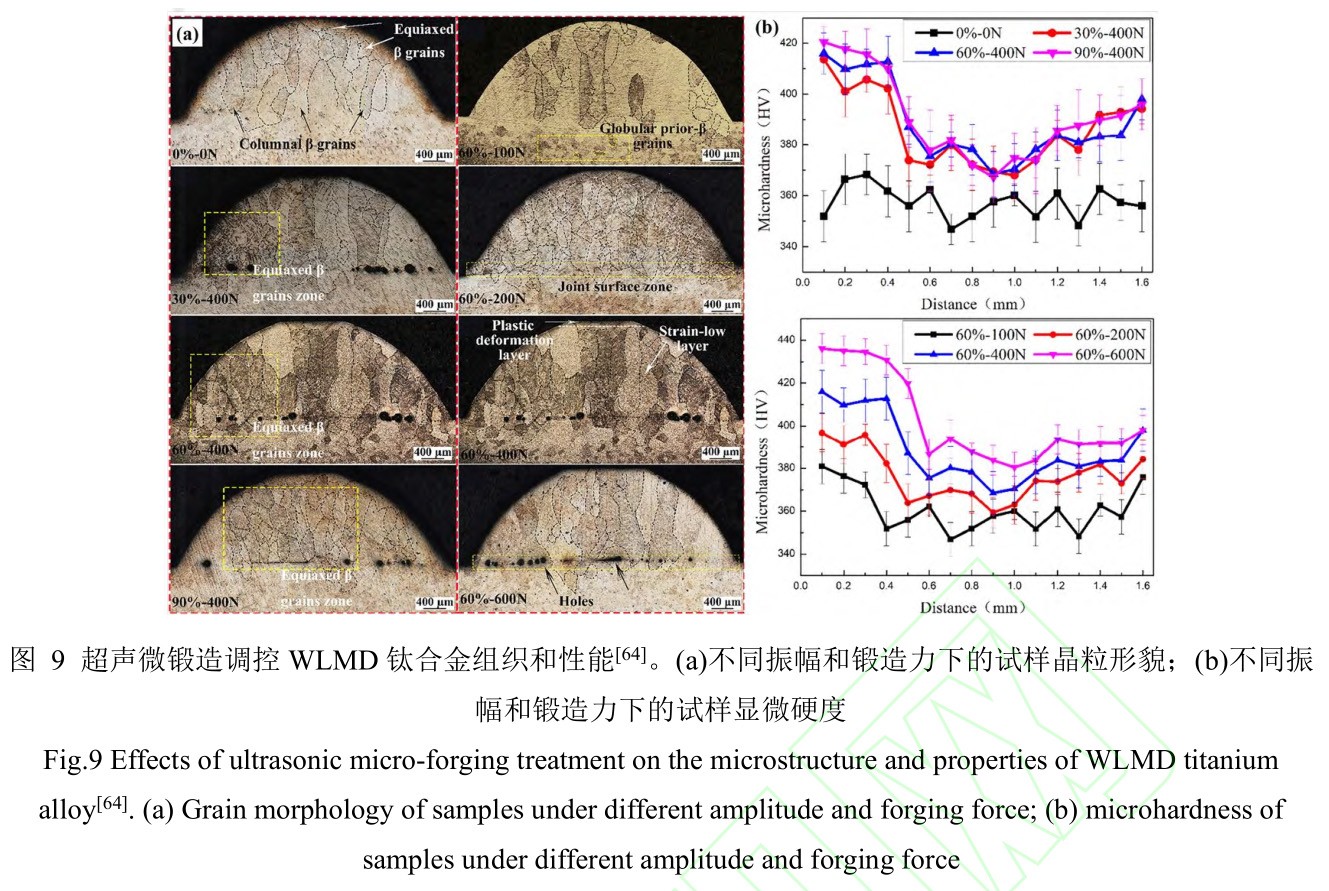
越來越多致力于鈦合金WLMD增材制造技術工程化應用的基礎研究正在持續(xù)開展。筆者研究團隊同樣注重發(fā)展WLMD基礎工藝和成形鈦合金組織性能優(yōu)化方法,并且基于新一代航空航天大型關鍵承力構件的一體化、輕量化和高可靠等設計使用要求,正在進行高效高精度激光增材制造技術的創(chuàng)新開發(fā),其中的關鍵科學問題和技術問題均涉及結構、材料、工藝、裝備等多因素的耦合、匹配及調控。
5、結論
相較于傳統(tǒng)鈦合金加工工藝,鈦合金WLMD具有節(jié)約原材料、降低生產(chǎn)成本、提高生產(chǎn)效率以及實現(xiàn)復雜結構成形等優(yōu)勢,是鈦合金現(xiàn)代制造技術的一個重要發(fā)展方向,并具有廣闊的研究價值和應用前景。但是,在沉積過程中還有復合成形工藝、成形件精度、表面質量、組織控制、應力控制和復雜路徑規(guī)劃等許多問題亟待解決,而正是這些因素的協(xié)同優(yōu)化決定了WLMD鈦合金成形件是否滿足工程應用的需求。WLMD技術未來應當著重面向航空航天大型復雜構件制造、太空金屬增材制造、艦載增材制造、水下激光修復等領域發(fā)揮其獨特優(yōu)勢。鈦合金WLMD具有豐富的科學內涵,總結發(fā)展現(xiàn)狀并思考其未來研究趨勢,主要結論和需進一步關注的方向如下:
(1)WLMD高效率和高精度復合增材制造。旁軸送絲WLMD受限于方向耦合問題,而發(fā)展同軸送絲WLMD工藝需要重點克服加工裝備集成設計的難題。此外,當前仍以單一激光成形鈦合金為主,但是受限于激光功率和成形質量的匹配性問題,WLMD成形效率仍有較大提升空間。為此,需研究增材制造過程中多波長激光集成、絲材-粉末多材料復合、多能場-多工藝的匹配協(xié)調機制,建立構件成形質量主動控制數(shù)學模型及控制策略,實現(xiàn)高功率激光送絲沉積、激光熔池動態(tài)整形以及激光送粉熔覆多工藝協(xié)同高效高精度分區(qū)制造。其中,為消除送絲方向性問題,可進一步開展新型同軸送絲技術的開發(fā),提高裝備和工藝穩(wěn)定性。
(2)WLMD過程組織缺陷識別、反饋與自調節(jié)。成形工藝對組織宏微觀形貌和應力分布影響顯著,為滿足工藝不斷優(yōu)化發(fā)展的需求,有必要對成形過程中的未熔合、裂紋和氣孔等缺陷進行監(jiān)測。為此,需構建一種高精度在線實時監(jiān)測與反饋優(yōu)化智能感知系統(tǒng),通過在線精準監(jiān)測裝置對多束高功率激光增材制造凝固成型的沉積層質量進行實時監(jiān)測,并結合高準確度離線檢測技術對比糾正,通過工藝調整、熔池整形、軌跡優(yōu)化及局部重熔等方法在線完成缺陷的主動控制,實現(xiàn)缺陷在線精準識別-實時診斷與反饋-缺陷主動抑制的閉環(huán)自調節(jié)。
(3)WLMD晶粒細化技術與相結構調控。WLMD沉積組織往往由粗大的β柱狀晶、晶界α相、晶內片層狀α集束以及少量馬氏體相組成,為了獲得較佳的性能參數(shù),需要建并完善材料-工藝-組織-性能的一體化設計、制造與調控理論及方法。為解決WLMD鈦合金組織的不均勻性,提高成形件綜合力學性能,可以從材料成分元素設計與控制,以及沉積工藝參數(shù)優(yōu)化與調控等方面入手;為解決(α+β)型鈦合金內部由于增材制造快速冷卻導致的亞穩(wěn)態(tài)馬氏體含量過多,可采用合適的后處理方式,包括引入顆粒、超聲沖擊和多重熱處理等方法,使馬氏體轉化為穩(wěn)定的α相,獲得更多網(wǎng)籃組織,提高合金的力學性能并改善各向異性。
參考文獻
[1] 林鑫, 黃衛(wèi)東. 應用于航空領域的金屬高性能增材制造技術[J]. 中國材料進展, 2015,34(9): 684-688.
Lin X, Huang W D. High performance metal additive manufacturing technology applied in aviation field[J]. Materials China, 2015, 34(9): 684-688.
[2] 湯海波, 吳宇, 張述泉, 等. 高性能大型金屬構件激光增材制造技術研究現(xiàn)狀與發(fā)展趨勢[J]. 精密成形工程, 2019, 11(4): 58-63.
Tang H B, Wu Y, Zhang S Q, et al. Research status and development trendof high performance large metallic components by laser additive manufacturing technique[J]. Journal of Netshape Forming Engineering, 2019, 11(4): 58-63.
[3] 顧冬冬, 張紅梅, 陳洪宇, 等. 航空航天高性能金屬材料構件激光增材制造[J]. 中國激光, 2020, 47(5): 0500002.
Gu D D, Zhang H M, Chen H Y, et al. Laser additive manufacturing of high-performance metallic aerospace components[J]. Chinese Journal of Lasers, 2020, 47(5): 0500002.
[4] Su J, Jiang F, Teng J, et al. Recent innovations in laser additive manufacturing of titanium alloys[J]. International Journal of Extreme Manufacturing, 2024, 6(3): 032001.
[5] 楊永強, 吳世彪, 張越, 等. 光纖激光器在金屬增材制造中的應用進展及展望[J]. 中國激光, 2020, 47(5): 0500012.
Yang Y Q, Wu S B, Zhang Y, et al. Application progress and prospect of fiber laser in metal additive manufacturing[J]. Chinese Journal of Lasers, 2020, 47(5): 0500012.
[6] 果春煥, 嚴家印, 王澤昌, 等. 金屬激光熔絲增材制造工藝的研究進展[J]. 熱加工工藝,2020, 49(16): 5-10.
Guo C H, Yan J Y, Wang Z C, et al. Research progress on metal laser fuse additive manufacturing process[J]. Hot Working Technology, 2020, 49(16): 5-10.
[7] 高海瑞, 李繼康, 張振武, 等. 多場調控金屬激光增材制造研究現(xiàn)狀與展望[J]. 中國激光, 2024, 51(10): 1002306.
Gao H R, Li J K, Zhang Z W, et al. Research status and prospect of multi-field modulated metal laser additive manufacturing[J]. Chinese Journal of Lasers, 51(10): 1002306.
[8] 宋波, 張金良, 章媛潔, 等. 金屬激光增材制造材料設計研究進展[J]. 金屬學報, 2023,59(1): 1-15.
Song B, Zhang J L, Zhang Y J, et al. Research progress of materials design for metal laser additive manufacturing[J]. Acta Metallurgica Sinica, 2023, 59(1): 1-15.
[9] Moeinfar K, Khodabakhshi F, Kashani-Bozorg S F, et al. A review on metallurgical aspects of laser additive manufacturing (LAM): Stainless steels, nickel superalloys, and titanium alloys[J].Journal of Materials Research and Technology, 2022, 16: 1029-1068.
[10] 周慶軍, 嚴振宇, 張京京, 等. 航天運載器大型金屬構件激光定向能量沉積研究及應用進展[J]. 中國激光, 2024, 51(10): 1002303.
Zhou Q J, Yan Z Y, Zhang J J, et al. Research and application progress of laser directed energy deposition on large-scale metal components in aerospace[J]. Chinese Journal of Lasers, 2024,51(10): 1002303.
[11] 馮啟高, 王琳鑫, 王磊, 等. 復合熱源鈦合金熔絲高質量增材制造工藝研究[J]. 中國激光, 2023, 50(8): 0802306.
Feng Q G, Wang L X, Wang L, et al. Research on high-quality additive manufacturing process of titanium alloy fuse with composite heat source[J]. Chinese Journal of Lasers, 2023, 50(8):0802306.
[12] Sacco E, Moon S K. Additive manufacturing for space: status and promises[J]. The International Journal of Advanced Manufacturing Technology, 2019, 105(10): 4123-4146.
[13] Ishfaq K, Asad M, Mahmood M A, et al. Opportunities and challenges in additive manufacturing used in space sector: a comprehensive review[J]. Rapid Prototyping Journal,2022, 28(10): 2027-2042.
[14] 房立家, 孫兵兵, 張強, 等. 激光選區(qū)熔化成形零件結構設計與分析[J]. 激光與光電子學進展, 2023, 60(5): 0514010.
Fang L J, Sun B B, Zhang Q, et al. Structural design and analysis of selective laser melting forming parts[J]. Laser & Optoelectronics Progress, 2023, 60(5): 0514010.
[15] 李光明, 朱剛賢, 李加強, 等. 激光內送粉變姿態(tài)增材制造薄壁墻的試驗研究[J]. 激光與光電子學進展, 2023, 60(1): 0114008.
Li G M, Zhu G X, Li J Q, et al. Experimental study on thin walls by laser additive manufacturing based inside-beam powder feeding with variable posture[J]. Laser &
Optoelectronics Progress, 2023, 60(1): 0114008.
[16] Ding X P, Li H M, Zhu J Q, et al. Application of infrared thermography for laser metal-wire additive manufacturing in vacuum[J]. Infrared Physics & Technology, 2017, 81: 166-169.
[17] Yuan D, Shao S, Guo C, et al. Grain refining of Ti-6Al-4V alloy fabricated by laser and wire additive manufacturing assisted with ultrasonic vibration[J]. Ultrasonics Sonochemistry, 2021,73: 105472.
[18] ?kerfeldt P, Antti M-L, Pederson R. Influence of microstructure on mechanical properties of laser metal wire-deposited Ti-6Al-4V[J]. Materials Science and Engineering: A, 2016, 674:428-437.
[19] Ding D, Pan Z, Cuiuri D, et al. Wire-feed additive manufacturing of metal components:technologies, developments and future interests[J]. The International Journal of Advanced Manufacturing Technology, 2015, 81(1): 465-481.
[20] Heralic A. Monitoring and control of robotized laser metal-wire deposition[M]. Sweden:Chalmers Tekniska Hogskola, 2012.
[21] Kuznetsov A, Jeromen A, Govekar E. Droplet detachment regimes in annular laser beam droplet generation from a metal wire[J]. CIRP Annals, 2014, 63(1): 225-228.
[22] Fu J, Gong L, Zhang Y, et al. Microstructure and Mechanical Properties of Ti-6Al-4V Fabricated by Vertical Wire Feeding with Axisymmetric Multi-Laser Source[J]. Applied Sciences, 2017, 7(3): 227.
[23] Mok S H, Bi G, Folkes J, et al. Deposition of Ti-6Al-4V using a high power diode laser and wire, Part I: Investigation on the process characteristics[J]. Surface and Coatings Technology,2008, 202(16): 3933-3939.
[24] Mok S H, Bi G, Folkes J, et al. Deposition of Ti-6Al-4V using a high power diode laser and wire, Part II: Investigation on the mechanical properties[J]. Surface and Coatings Technology, 2008, 202(19): 4613-4619.
[25] Moures F, Cical? E, Sallamand P, et al. Optimisation of refractory coatings realised with cored wire addition using a high-power diode laser[J]. Surface and Coatings Technology, 2005,200(7): 2283-2292.
[26] Kim J-D, Peng Y. Plunging method for Nd:YAG laser cladding with wire feeding[J]. Optics and Lasers in Engineering, 2000, 33(4): 299-309.
[27] Syed W U H, Pinkerton A J, Li L. A comparative study of wire feeding and powder feeding in direct diode laser deposition for rapid prototyping[J]. Applied Surface Science, 2005, 247(1):268-276.
[28] Yang G, Ma J, Carlson B E, et al. Decreasing the surface roughness of aluminum alloy welds fabricated by a dual beam laser[J]. Materials & Design, 2017, 127: 287-296.
[29] Sun J, Sekou S. Investigation on the process characteristics of laser cladding fabrication using 45 carbon steel wire[J]. Advanced Materials Research, 2012, 499: 147-151.
[30] Shen F, Tao W, Li L, et al. Effect of microstructure on the corrosion resistance of coatings by extreme high speed laser cladding[J]. Applied Surface Science, 2020, 517: 146085.
[31] Mortello M, Casalino G. Transfer mode effects on Ti6Al4V wall building in wire laser additive manufacturing[J]. Manufacturing Letters, 2021, 28: 17-20.
[32] 王涵, 周偉民, 閔國全, 等. 送絲激光增材制造的研究進展[J]. 中國金屬通報, 2018, 12:248-251.
Wang H, Zhou W M, Min G Q, et al. Research progress of wire feed laser additive manufacturing[J]. China Metal Bulletin, 2018, 12: 248-251.
[33] 陳源, 姜夢, 陳曦, 等. 光絲同軸激光增材制造研究進展[J]. 材料科學與工藝, 2022,30(2): 16-27.
Chen Y, Jiang M, Chen X, et al. Research progress of coaxial laser wire additive manufacturing[J]. Materials Science and Technology, 2022, 30(2): 16-27.
[34] 張吉平, 石世宏, 蔣偉偉, 等. 三光束光內送絲激光熔覆溫度場仿真分析與工藝優(yōu)化[J].中國激光, 2019, 46(10): 1002004.
Zhang J P, Shi S H, Jiang W W, et al. Simulation analysis of temperature field and process optimization of laser cladding based oninternal wire feeding of three beams[J]. Chinese Journal of Lasers, 2019, 46(10): 1002004.
[35] Ding X, Ma H, Zhang Q, et al. Effect of annealing heat treatment on microstructure and corrosion behavior of Ti6Al4V alloy fabricated by multi-laser beam wire-feed additive manufacturing in vacuum environment[J]. Journal of Alloys and Compounds, 2022, 914:165363.
[36] Motta M, Demir A G, Previtali B. High-speed imaging and process characterization of coaxial laser metal wire deposition[J]. Additive Manufacturing, 2018, 22: 497-507.
[37] Ji S, Liu F, Shi T, et al. Effects of defocus distance on three-beam laser internal coaxial wire cladding[J]. Chinese Journal of Mechanical Engineering, 2021, 34(04): 67-88.
[38] 戰(zhàn)金明, 梁志剛, 黃進鈺, 等. TC4 鈦合金表面單道激光熔覆工藝研究[J]. 應用激光,2020, 40(6): 955-961.
Zhan J M, Liang Z G, Huang J Y, et al. Study on the single laser cladding process on TC4 titanium alloy surface[J]. Applied Laser, 2020, 40(6): 955-961.
[39] Roch C, Tournier C, Lavernhe S. Process based modelling of power density for wire laser additive manufacturing using a coaxial head[J]. Additive Manufacturing, 2023, 73: 103648.
[40] Kelbassa J, Gasser A, Bremer J, et al. Equipment and process windows for laser metal deposition with coaxial wire feeding[J]. Journal of Laser Applications, 2019, 31(2): 022320.
[41] Churruca M M, Arrizabalaga J L, Garmendia I, et al. Comparative study of laser metal deposition (LMD) of coaxial wire and powder in the manufacture of Ti-6Al-4V structures[J].Dyna, 2020, 95(1): 376-379.
[42] Silze F, Schnick M, Sizova I, et al. Laser metal deposition of Ti-6Al-4V with a direct diode laser set-up and coaxial material feed[J]. Procedia Manufacturing, 2020, 47: 1154-1158.
[43] 符成學, 雷小偉, 賈曉飛, 等. 鈦合金激光增材制造技術研究與應用進展[J]. 焊管, 2023,46(8): 11-18.
Fu C X, Lei X W, Jia X F, et al. Research and application progress of titanium alloy laser additive manufacturing technology[J]. Welded Pipe and Tube, 2023, 46(8): 11-18.
[44] Du F, Zhu J, Ding X, et al. Dimensional characteristics of Ti-6Al-4V thin-walled parts prepared by wire-based multi-laser additive manufacturing in vacuum[J]. Rapid Prototyping Journal,2019, 25(5): 849-856.
[45] Liu S, Shin Y C. Additive manufacturing of Ti6Al4V alloy: A review[J]. Materials & Design,2019, 164: 107552.
[46] Baufeld B, Brandl E, Van Der Biest O. Wire based additive layer manufacturing: Comparison of microstructure and mechanical properties of Ti-6Al-4V components fabricated by laser-beam deposition and shaped metal deposition[J]. Journal of Materials Processing Technology,2011, 211(6): 1146-1158.
[47] Sun W, Shan F, Zong N, et al. Simulation of solidified β grain for Ti–6Al–4V during wire laser additive manufacturing by three-dimensional cellular automaton method[J]. Modelling and Simulation in Materials Science and Engineering, 2021, 29(6): 065006.
[48] Liu S, Brice C, Zhang X. Interrelated process-geometry-microstructure relationships for wire-feed laser additive manufacturing[J]. Materials Today Communications, 2022, 31: 103794.
[49] Yin J, Peng G, Chen C, et al. Thermal behavior and grain growth orientation during selective laser melting of Ti-6Al-4V alloy[J]. Journal of Materials Processing Technology, 2018, 260:57-65.
[50] Wilson-Heid A E, Wang Z, Mccornac B, et al. Quantitative relationship between anisotropic strain to failure and grain morphology in additively manufactured Ti-6Al-4V[J]. Materials Science and Engineering: A, 2017, 706: 287-294.
[51] Mantri S A, Banerjee R. Microstructure and micro-texture evolution of additively manufactured β-Ti alloys[J]. Additive Manufacturing, 2018, 23: 86-98.
[52] Liu Z, Welsch G. Literature survey on diffusivities of oxygen, aluminum, and vanadium in alpha titanium, beta titanium, and in rutile[J]. Metallurgical Transactions A, 1988, 19(4): 1121-1125.
[53] Ahmed T, Rack H J. Phase transformations during cooling in α+β titanium alloys[J].Materials Science and Engineering: A, 1998, 243(1): 206-211.
[54] 張大越, 伍新澤, 王一甲, 等. 激光熔絲 Ti6Al4V 合金成形工藝、微觀組織及強韌性研究[J]. 鋼鐵釩鈦, 2024, 45(1): 49-56.
Zhang D Y, Wu X Z, Wang Y J, et al. Forming process, microstructure, strength and toughness of Ti6Al4V alloy by laser wire-feed additive manufacturing[J]. Iron Steel Vanadium Titanium,2024, 45(1): 49-56.
[55] Simonelli M, Tse Y Y, Tuck C. On the texture formation of selective laser melted Ti-6Al-4V[J].Metallurgical and Materials Transactions A, 2014, 45(6): 2863-2872.
[56] Guo J, Liu Y, Zhao Y, et al. Tailoring microstructure and mechanical anisotropy of laser-MIG hybrid additive manufacturing TC11 titanium alloy through solution aging treatment[J].Journal of Materials Science, 2024: 1-18.
[57] Guo N, Wu D, Yu M, et al. Microstructure and properties of Ti-6Al-4V titanium alloy prepared by underwater wire feeding laser deposition[J]. Journal of Manufacturing Processes, 2022, 73:269-278.
[58] Srinivas M, Babu B S. A critical review on recent research methodologies in additive manufacturing[J]. Materials Today: Proceedings, 2017, 4(8): 9049-9059.
[59] Chen Y, Chen X, Jiang M, et al. Coaxial laser metal wire deposition of Ti6Al4V alloy: process,microstructure and mechanical properties[J]. Journal of Materials Research and Technology,2022, 20: 2578-2590.
[60] Xie Y, Gao M, Wang F, et al. Anisotropy of fatigue crack growth in wire arc additive manufactured Ti-6Al-4V[J]. Materials Science and Engineering: A, 2018, 709: 265-269.
[61] Pixner F, Warchomicka F, Peter P, et al. Wire-Based Additive Manufacturing of Ti-6Al-4V Using Electron Beam Technique[J]. Materials, 2020, 13(15): 3310.
[62] Graf B, Marko A, Petrat T, et al. 3D laser metal deposition: process steps for additive manufacturing[J]. Welding in the World, 2018, 62(4): 877-883.
[63] 任朝暉, 劉振, 周世華, 等. 鈦合金激光熔絲增材制造的溫度場與應力場模擬[J]. 東北大學學報(自然科學版), 2020, 41(04): 551-556.
Ren Z H, Liu Z, Zhou S H, et al. Temperature field and stress field simulation of titanium alloy laser fuse additive manufacturing[J]. Journal of Northeastern University (Natural Science),2020, 41(04): 551-556.
[64] Ye H, Ye K, Guo B, et al. Effects of combining ultrasonic micro-forging treatment with laser metal wire deposition on microstructural and mechanical properties in Ti-6Al-4V alloy[J].Materials Characterization, 2020, 162: 110187.
[65] Yang Y, Jin X, Liu C, et al. Residual stress, mechanical properties, and grain morphology of Ti-6Al-4V alloy produced by ultrasonic impact treatment assisted wire and arc additive manufacturing[J]. Metals, 2018, 8(11): 934.
[66] Donoghue J, Antonysamy A A, Martina F, et al. The effectiveness of combining rolling deformation with wire–arc additive manufacture on β-grain refinement and texture modification in Ti-6Al-4V[J]. Materials Characterization, 2016, 114: 103-114.
[67] Sabban R, Bahl S, Chatterjee K, et al. Globularization using heat treatment in additively manufactured Ti-6Al-4V for high strength and toughness[J]. Acta Materialia, 2019, 162: 239-254.
[68] Jiang X J, Chen G Y, Men X L, et al. Ultrafine duplex microstructure and excellent mechanical properties of TC4 alloy via a novel thermo-mechanical treatment[J]. Journal of Alloys and Compounds, 2018, 767: 617-621.
[69] 張穎, 胡生雙, 鄭超, 等. 雙重退火對激光增材制造 TC18 鈦合金組織和性能的影響[J].特種鑄造及有色合金, 2021, 41(8): 1006-1009.
Zhang Y, Hu S S, Zheng C, et al. Effects of double annealing on microstructure and properties of TC18 titanium alloy by laseradditive manufacturing[J]. Special Casting & Nonferrous Alloys, 2021, 41(8): 1006-1009.
[70] 高伶俐, 劉金旭, 李遠, 等. 電脈沖短時熱處理對等軸組織熱軋 TC4 組織轉變和絕熱剪切特性的影響[J]. 稀有金屬材料與工程, 2016, 45(8): 2150-2154.
Gao L L, Liu J X, Li Y, et al. Effect of short time heat treatment with electric pulse on microstructure transformation and adiabatic shear characteristics of hot rolling TC4[J]. Rare Metal Materials and Engineering, 2016, 45(8): 2150-2154.
[71] Zhao Z, Wang G, Zhang Y, et al. Fast recrystallization and phase transformation in ECAP deformed Ti-6Al-4V alloy induced by pulsed electric current[J]. Journal of Alloys and Compounds, 2019, 786: 733-741.
無相關信息