前言
鈦在地球上的儲量十分豐富,在金屬元素中位列第七。以鈦為主要元素的鈦合金有很多優(yōu)點,其中以TC4鈦合金用途最廣,而且相對于其它合金來說,因其具有質(zhì)量輕、耐腐蝕性好、比強度高、彈性模量低、生物相容性好等被廣泛應(yīng)用于航空航天[1]、海洋船舶[2]、生物醫(yī)藥[3]等領(lǐng)域。然而鈦合金本身的耐腐蝕性較差,尤其是在海洋環(huán)境的惡劣條件下,海水中含有大量的氧化性Cl-,使其比普通水環(huán)境更具腐蝕性,純鈦合金的防腐性能達不到所需的要求,這使得鈦及其合金零部件在高鹽、高濕的海洋環(huán)境中工作時,會遭受嚴重的電化學(xué)腐蝕和縫隙腐蝕,極大的限制了它的大規(guī)模應(yīng)用[4]。雖然依靠其表面自身的氧化膜,鈦合金具有一定的耐腐蝕性,但自然形成的氧化膜較薄,易被破壞,導(dǎo)致其耐腐蝕性能有限。為了增強其耐腐蝕性,提高在海洋環(huán)境中的使用壽命,鈦合金表面處理是一種有效的方法。近些年來發(fā)展起來的微弧氧化技術(shù)(Micro-arcoxidation,MAO)因其綠色環(huán)保、操作簡單、膜層與基體結(jié)合力強且膜層致密的優(yōu)點而被廣泛應(yīng)用于鎂、鋁、鈦等金屬表面處理中[5-7]。
微弧氧化技術(shù)可以在鈦合金表面生成可控的致密氧化陶瓷膜,以減緩腐蝕。但是微弧氧化處理會在鈦合金基體表面留下較多的孔洞及裂紋,抑制了其耐腐蝕性能的進一步提高。近年來,許多學(xué)者通過封孔方法來提高微弧氧化膜的耐腐蝕性,包括在微弧氧化電解液中加入不溶性的微納米粒子:氧化石墨烯[8-10]、氮化硼[11-13]、碳納米管[14-16]、碳化硅[17-19]氮化硅[20-22]、聚四氟乙烯[23-24]、氧化鋅[25-26]等進行原位封孔,或者通過微弧氧化技術(shù)與其它表面處理技術(shù)相結(jié)合的后封孔方法。BA等[27]采用微弧氧化與水熱生長相結(jié)合的方法,在微弧氧化后的鎂合金表面原位生長插有肉豆蔻酸離子的水滑石膜,微弧氧化膜中的微孔被水滑石封閉,表面變得疏水,復(fù)合涂層最低腐蝕電流密度較基體降低了5個數(shù)量級,明顯提高了鎂合金的耐腐蝕性能。于浩洋等[28]采用微弧氧化和溶膠凝膠結(jié)合的方法,在NiTi合金表面先摻雜ZnO微粒進行微弧氧化,后利用聚丙烯酰胺溶膠凝膠進行封孔處理,提高了NiTi合金的耐腐蝕性,且在潮濕的條件下具有一定的自修復(fù)能力。莫格等[29]在微弧氧化后的鎂合金上涂裝聚苯胺改性的環(huán)氧樹脂,所制得的復(fù)合涂層腐蝕電流密度下降了3個數(shù)量級,顯著提高了復(fù)合涂層對鎂合金基體的腐蝕防護能力。HE等[30]結(jié)合微弧氧化和激光加工技術(shù)在S355海洋鋼表面制備了復(fù)合涂層,該復(fù)合涂層與基體層結(jié)合良好,具有良好的力學(xué)性能;當(dāng)微弧氧化的電流密度為5A.dm?2時,復(fù)合涂層的耐腐蝕性最好,腐蝕電流降低了3個數(shù)量級。
受自然界啟發(fā),研究者發(fā)現(xiàn)在材料表面構(gòu)建超疏水膜可以減少水溶性腐蝕介質(zhì)與基體的接觸,從而減少腐蝕[31]。周塏杰等[32]在鎂合金表面涂覆環(huán)氧樹脂粘結(jié)層,再向其噴涂微米二氧化硅顆粒和納米聚四氟乙烯顆粒構(gòu)建超疏水膜,其具有優(yōu)異的耐腐蝕性能以及自清潔、防污特性。楊文廣等[33]在鋁合金表面制備鎂鋁水滑石膜,并用全氟辛基三乙氧基硅烷修飾,制備出耐腐蝕性能優(yōu)異的超疏水膜。很多研究者采用微弧氧化技術(shù)結(jié)合低表面能物質(zhì)自組裝在鎂、鋁合金表面構(gòu)建超疏水膜來提高其耐腐蝕性能[34-35],但在鈦合金上的相關(guān)研究較少?;诖?,本研究采用微弧氧化技術(shù),在TC4鈦合金表面構(gòu)建微納米結(jié)構(gòu),并采用十八烷基三甲氧基硅烷(Octadecyltrimethoxysilane,OTMS)進行表面修飾,既對微弧氧化膜層起到封孔作用,又賦予其低表面能,從而在其表面形成了一層長效耐久的抗腐蝕超疏水膜,有效提高了鈦合金的耐腐蝕性能,在鈦合金表面防護方面具有廣闊的應(yīng)用前景。
1、試驗
1.1鈦合金預(yù)處理
TC4鈦合金購自東莞市宏迪金屬材料有限公司,其主要成分(質(zhì)量分數(shù))為6%Al、4%V、0.3%Fe、0.01%C、0.03%O,其余為Ti。將直徑為15mm、厚度為1.5mm的圓形試樣依次用800、1000、1500、2000目SiC砂紙打磨,去除表面氧化膜,并用無水乙醇和去離子水分別超聲清洗10min,自然晾干。
1.2超疏水微弧氧化膜的制備
將預(yù)處理后的TC4鈦合金試樣放入3L的10g/L九水偏硅酸鈉、10g/L十二水磷酸三鈉和2g/L氫氧化鉀的混合溶液中進行微弧氧化。采用直流脈沖電源,試樣接電源正極,不銹鋼電解液槽接電源負極,具體工藝參數(shù)為:恒流模式,電流密度為18A/dm2,脈沖頻率為500Hz,占空比為20%,氧化時間為20min。使用機械攪拌和循環(huán)冷卻裝置保持電解液溫度在50℃以下。微弧氧化試驗完成后,取出樣品,并用去離子水沖洗,晾干備用,命名為Ti-MAO。
將微弧氧化后的樣品在室溫下浸入OTMS乙醇溶液(OTMS、去離子水、乙醇按1:1:18的體積比配制,靜置4h)中1h,取出后在120℃下固化2h,制備流程如圖1所示,所得樣品命名為
Ti-MAO-OTMS。作為對照,將預(yù)處理的鈦合金試樣直接浸入OTMS溶液中1h并在同樣條件下固化,命名為Ti-OTMS。
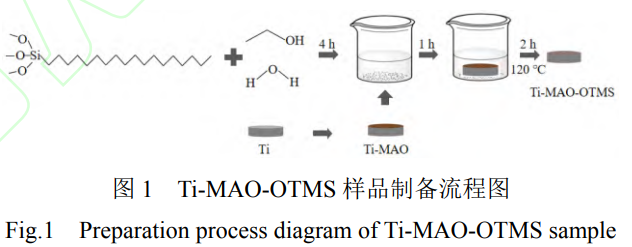
1.3性能表征
采用掃描電子顯微鏡(SEM,JSM-IT100,JEOL)對樣品表面形貌進行觀察。并利用所配備的能量分散譜儀(EDS)確定樣品表面成分。使用傅立葉變換紅外衰減全反射光譜儀(FTIRATR,NicoletIS1,ThermoFisher)對樣品的官能團進行分析。通過X射線粉末衍射儀(XRD,MAX2500VB3+/PC,Rigaku)分析微弧氧化膜的結(jié)構(gòu)。使用接觸角測量儀(JC2000D1,POWEREACH)表征涂層的潤濕性。每次使用5μL的水滴,在不同位置至少重復(fù)5次,取其平均值。利用光學(xué)輪廓儀(ContourGTK0)測試樣品表面粗糙度(Ra),測試范圍為241μm×180.8μm。
采用電化學(xué)站(CHI660E,武漢辰華)進行電化學(xué)測試。所有試驗均采用常規(guī)的三電極電化學(xué)方法進行,其中飽和甘汞電極作為參比電極,鉑電極作為對電極,試樣作為工作電極。用硅橡膠密封試樣,留下10mm×10mm的面積。在測試之前,鈦合金試樣在3.5wt%的NaCl溶液中浸泡30min。電化學(xué)測試主要包括動電位極化和電化學(xué)阻抗測量。掃描速率為5mV/s,電位范圍為-1~1V進行動電位極化。同時使用塔菲爾外推法計算了腐蝕電流密度(icorr)、腐蝕電位(Ecorr)并計算出腐蝕速率(Pi),在0.01Hz和100kHz之間進行電化學(xué)阻抗測量,并用Z-View軟件對測試結(jié)果進行擬合。
2、結(jié)果與討論
2.1表面形貌和組成分析
圖2為不同樣品的SEM圖。從圖2a中可以看出,鈦合金基體經(jīng)過SiC砂紙打磨后,表面平整,其表面Ra值僅為0.28μm。圖2b中,鈦合金經(jīng)微弧氧化后表面出現(xiàn)很多微凸起及小的裂縫,微凸起尺寸在幾到幾十微米不等,Ra值增大到5.09μm。這主要是因為MAO反應(yīng)過程中的火花放電階段會在鈦合金表面形成大量的放電通道,熔融態(tài)的氧化物以類似火山噴發(fā)的方式從這些通道中大量噴濺而出,遇到溫度低的電解液驟冷形成氧化物陶瓷膜[36]。由于放電順序的不同,MAO涂層表面呈現(xiàn)連續(xù)多孔的島狀分布。從圖2b中Ti-MAO的高放大倍數(shù)SEM圖可以明顯看出,鈦合金經(jīng)微弧氧化后表面出現(xiàn)了納米級的小凸起及放電通道留下的孔洞,為超疏水膜的構(gòu)建提供了可能。從圖2c可以看出,Ti-MAO-OTMS表面形貌沒有明顯變化,但是其表面裂縫明顯減少,部分孔洞被填充,而且其Ra值降低到3.86μm,這可能是因為OTMS可以較好的填充進微弧氧化的裂縫及孔洞進行封孔。
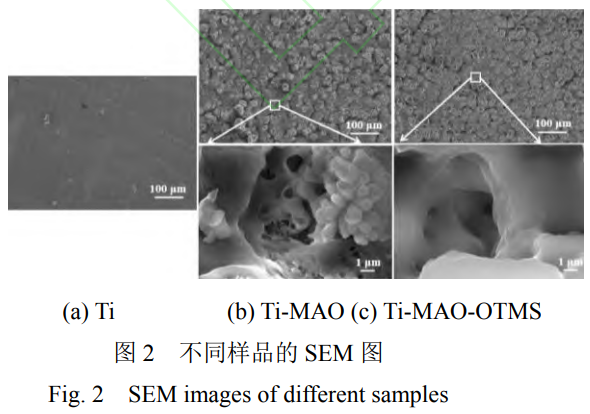
Ti-MAO的FT-IR譜圖中1080cm-1處的峰對應(yīng)于硅氧鍵的伸縮振動峰(圖3),來源于溶液中的硅酸鹽轉(zhuǎn)化的SiO2。相比于Ti-MAO,Ti-MAO-OTMS的FT-IR譜圖中新出現(xiàn)的2920cm-1和2850cm-1處的峰分別對應(yīng)亞甲基基團的非對稱振動峰和對稱伸縮振動峰,進一步證明了OTMS的成功引入。
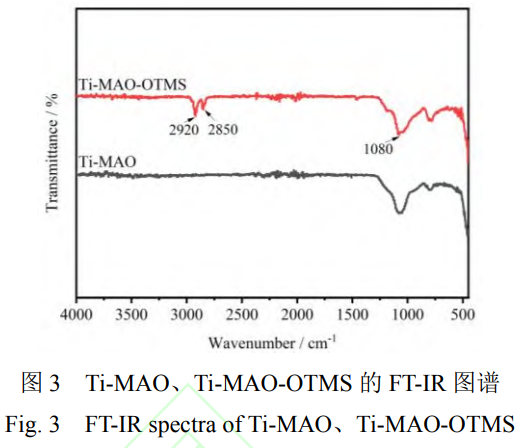
圖4為鈦合金微弧氧化前后的XRD圖??梢钥闯?,在25.5°和27.6°處分別為TiO2的銳鈦礦相(101)和金紅石相(110)的衍射峰。Ti-MAO中的15°-35°
范圍內(nèi)出現(xiàn)了寬峰值,說明涂層中有一些非晶相存在。結(jié)合表1中試樣表面元素質(zhì)量百分比可知,純鈦合金基體主要以Ti元素為主,其中夾雜著少量的Al、V等元素。而Ti-MAO樣品中Ti元素含量明顯減少,O、Si元素含量明顯增加,結(jié)合圖3中Ti-MAO的FT-IR特征峰,表明該寬峰為非晶相的SiO2的衍射。在反應(yīng)的進行中,電解液中的SiO32-在電場的作用下向陽極方向移動,并轉(zhuǎn)化為SiO2。電解質(zhì)的迅速冷卻能夠使涂層以較高的冷卻速率生長,其中SiO2以非晶形式存在于涂層中[37]。說明TC4鈦合金經(jīng)過微弧氧化后主要由Ti、銳鈦礦TiO2、金紅石TiO2和非晶相的SiO2組成,TiO2相主要源于基體中的Ti在微弧氧化過程中的氧化。將TC4鈦合金作為陽極置于微弧氧化電解液中連通電源時,兩極之間產(chǎn)生電場,電解液中的陰離子在電場的作用下向陽極遷移,陽離子向陰極遷移,到達兩極表面之后通過得失電子主要發(fā)生如下電化學(xué)反應(yīng):
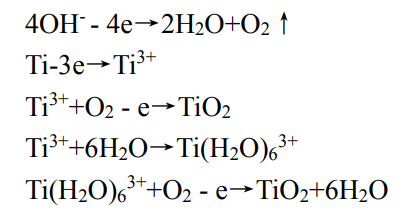
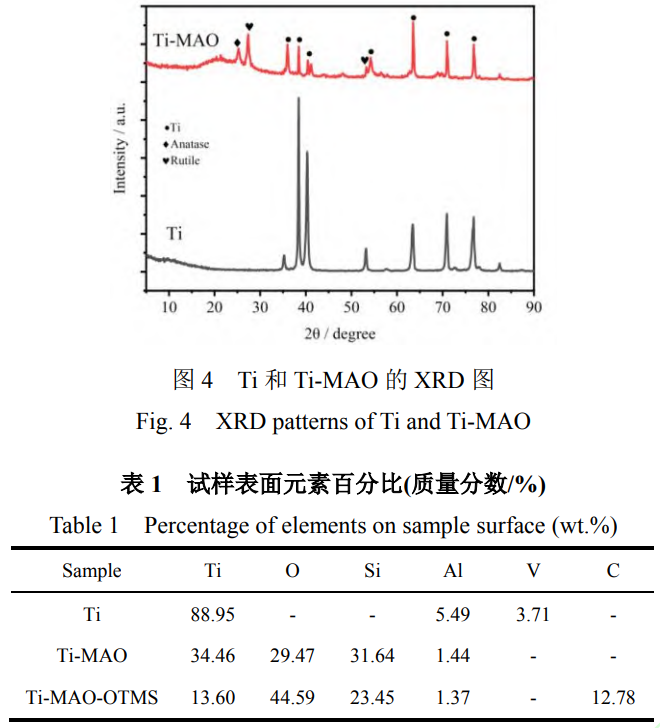
2.2表面潤濕性能分析
從圖5a可知,Ti的接觸角為48°±2°,表現(xiàn)出親水性。經(jīng)微弧氧化處理后Ti-MAO的接觸角小于2°(圖5b),表現(xiàn)出超親水性。這主要歸因于微弧氧化之后表面出現(xiàn)的微納米粗糙結(jié)構(gòu)。圖5c中Ti-OTMS的接觸角為110°±1.5°,說明其具有疏水性。而Ti-MAO-OTMS的接觸角為154°±1.8°(圖5d),而且其滾動角約為3°±1°,表現(xiàn)出超疏水性。這主要歸因于鈦合金基體表面微納米結(jié)構(gòu)的構(gòu)建和低表面能物質(zhì)OTMS的成功修飾。疏水性的提高有利于改善其耐腐蝕性。
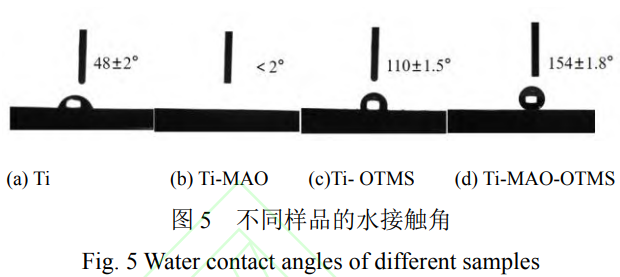
2.3防腐性能分析
從圖6a的Bode阻抗圖可以看出Ti-MAO-OTMS涂層低頻下的阻抗模量(|Hz0.01|)比Ti和Ti-MAO高了約兩個數(shù)量級,達到4.97×107Ω。結(jié)合圖6b中Tafel極化曲線和表2所示的擬合電參數(shù),可以看出相比于Ti,Ti-MAO的Ecorr提升了0.416V,icorr降低了約2個數(shù)量級,達到了6.893×10-8A·cm-2。這歸因于微弧氧化膜內(nèi)部致密層的阻擋作用。而經(jīng)過OTMS修飾的Ti-MAO-OTMS的Ecorr提高了0.934V,達到0.454V;icorr降低了近4個數(shù)量級,達到了9.481×10-10A·cm-2。經(jīng)過超疏水膜層修飾后,其Pi較純鈦合金降低了3個數(shù)量級。圖6c為不同樣品的Nyquist圖。一般來說,Nyquist圖中容抗弧直徑越大,說明膜的耐蝕性能越好[38]??梢钥闯?,鈦合金基體Ti容抗弧直徑最小,具有最差的耐腐蝕性。
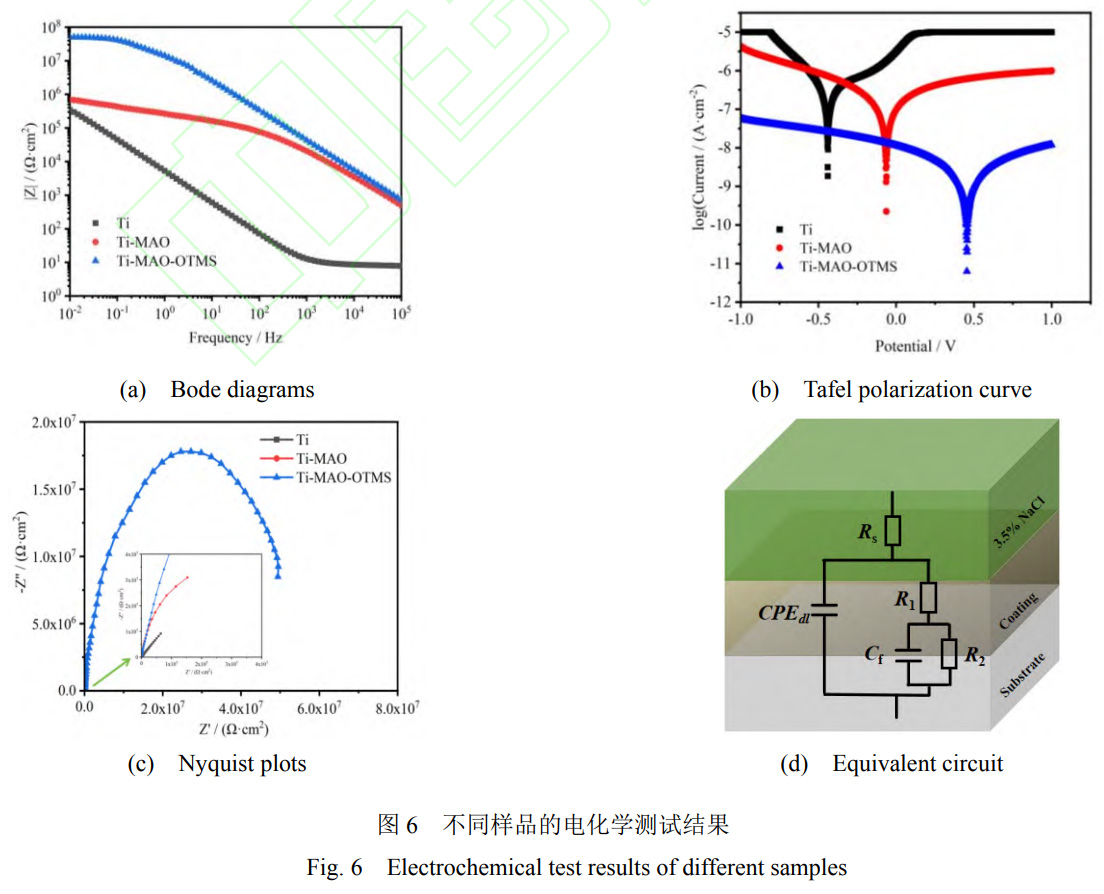
Ti-MAO樣品的容抗弧直徑有所增大,說明其耐腐蝕性有所提高。由于Ti-MAO表面較多的微孔和裂紋有利于腐蝕性離子的滲入,使其耐腐蝕性提高有限。而Ti-MAO-OTMS樣品的容抗弧直徑明顯進一步增大,說明其具有最佳的耐腐蝕性。這歸因于其優(yōu)異的超疏水性能,有效阻擋了Cl-等腐蝕性物質(zhì)對基體造成的損傷。為了進一步分析樣品在3.5wt%NaCl溶液中的電化學(xué)性能,使用圖6d所示的等效電路擬合電化學(xué)阻抗譜,具體參數(shù)如表3所示。Rs為溶液電阻,R1和CPEdl分別表示電解質(zhì)溶液與膜層/基底之間的電阻和雙電層電容。R2和Cf分別為電阻和膜層在表面的電容。R1值越高,耐腐蝕性越好。
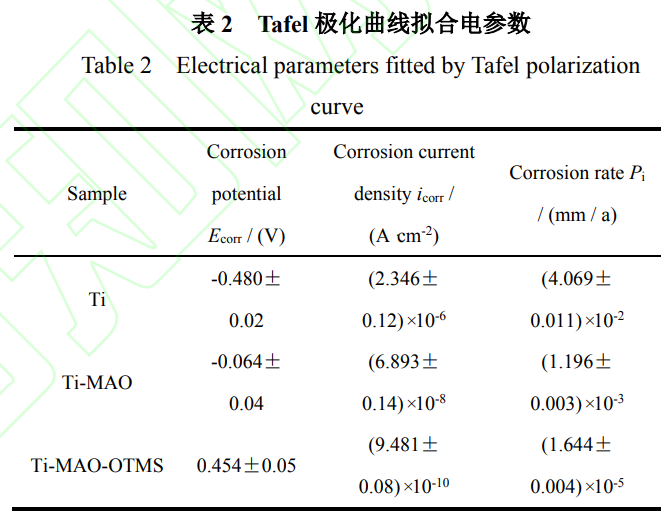
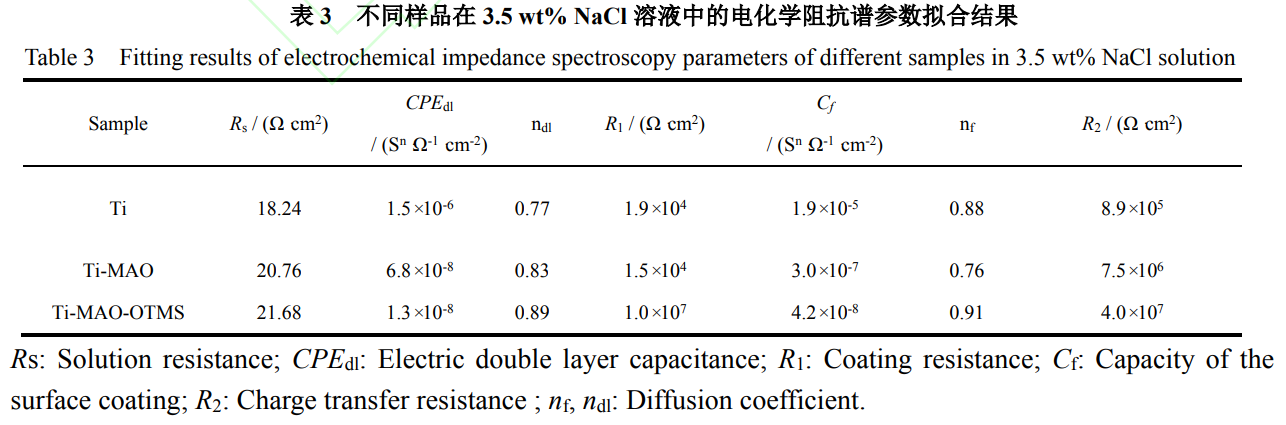
由表3中的數(shù)據(jù)可知,樣品Ti的R2遠大于R1,說明鈦合金基體的耐蝕性主要由鈍化膜決定。樣品Ti-MAO的R1相對于Ti的R1有所降低,這是由于微弧氧化后試樣表面變成超親水,腐蝕溶液中的腐蝕介質(zhì)更容易與試樣表面接觸,更容易完成吸附過程。然而,Ti-MAO的膜層電阻R2比基體增大近10倍,這證明了微弧氧化后TiO2膜層內(nèi)部密度更大,使得微弧氧化樣品的表面耐腐蝕性優(yōu)于未經(jīng)處理的基體樣品。微弧氧化后的樣品經(jīng)低表面能物質(zhì)修飾后,樣品表面由超親水性變?yōu)槌杷?,Ti-MAO-OTMS的R2相對于基體增大將近50倍。由于膜層的超疏水性,R1比未處理的基體提高了約500倍,比微弧氧化后的樣品提高約700倍。因為超疏水表面將腐蝕介質(zhì)與樣品表面分開,使得超疏水試樣表面的耐蝕性優(yōu)于基體和僅微弧氧化處理后的試樣。通過以上電化學(xué)分析可以看出,與純鈦合金基體相比,鈦合金微弧氧化結(jié)合OTMS修飾得到的復(fù)合膜明顯提高了基體的耐蝕性,且防腐效果顯著優(yōu)于單一的微弧氧化膜。
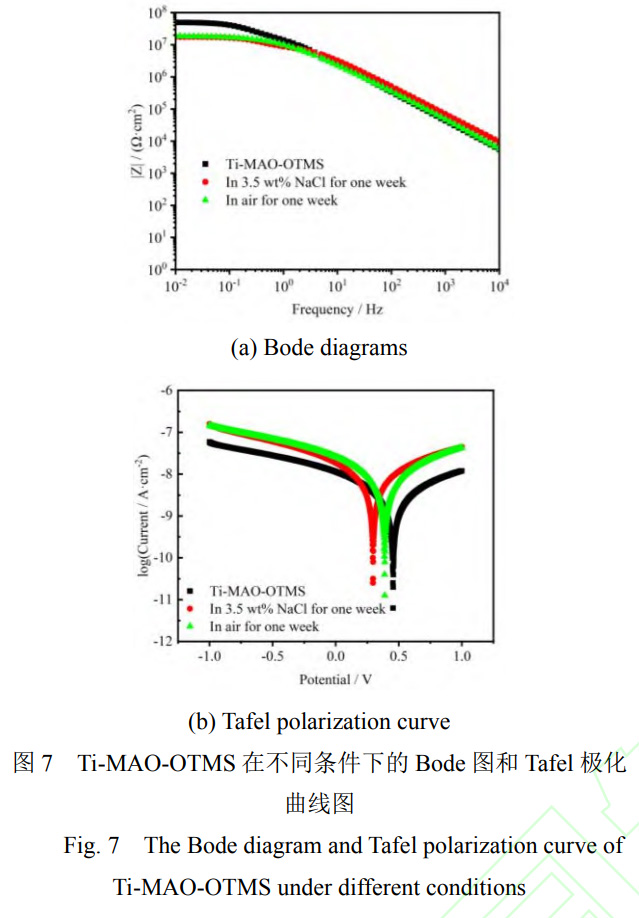
研究了Ti-MAO-OTMS樣品的腐蝕耐久性,結(jié)果如圖(7a、7b)所示??梢钥闯?,Ti-MAO-OTMS分別在3.5wt%NaCl溶液中浸泡和在空氣中暴露一周后,其阻抗值略有下降,但仍都能達到107數(shù)量級。在3.5wt%NaCl溶液中浸泡一周后其阻抗值略有下降,但仍都能達到107數(shù)量級。在3.5wt%NaCl溶液中浸泡一周后,樣品的Ecorr為0.296V,icorr仍能達到2.555×10-9A·cm-2,而且其水接觸角變?yōu)?45°±1.5°,仍然具有較強的疏水性(圖8a);室溫下在空氣中暴露一周后,空氣中的水分、氧氣及腐蝕性介質(zhì)的聯(lián)合作用會引起膜的破壞,導(dǎo)致其耐腐蝕性能有所下降,樣品的Ecorr為0.388V,icorr為2.698×10-9A·cm-2,仍然具有優(yōu)異的耐腐蝕性,而且其表面仍然具有超疏水性能,其水接觸角為152°±2°(圖8b)。表明其具有優(yōu)異的腐蝕耐久性。
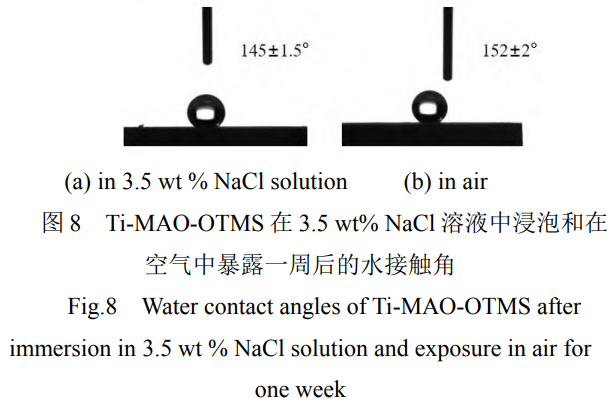
圖9所示為鈦合金表面超疏水膜的耐腐蝕機理示意圖。圖9a為鈦合金基體直接與NaCl溶液接觸,由于表面只有一層薄的天然氧化膜且是親水的,使腐蝕性液體很容易吸附在樣品表面,對樣品造成破壞。而圖9b中的Ti-MAO-OTMS表面獲得了低表面能的微納粗糙結(jié)構(gòu),可以捕獲空氣并在樣品表面形成空氣層,使其具有超疏水性。大大減小了腐蝕性的Cl-等與試樣表面的接觸,延緩和減少了Cl-等在試樣表面的吸附過程,從而提高了鈦合金在含腐蝕性Cl-等溶液中的耐腐蝕。
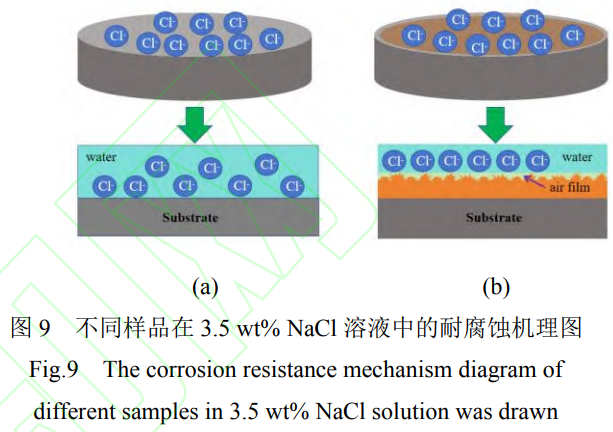
3、結(jié)論
(1)通過微弧氧化技術(shù)在TC4鈦合金表面構(gòu)建了以銳鈦礦和金紅石TiO2為主要成分的陶瓷膜,阻擋了水和腐蝕性離子的侵入,使鈦合金的耐腐蝕性能有所改善。與鈦合金基體相比,其腐蝕速率下降了1個數(shù)量級,自腐蝕電流密度下降了2個數(shù)量級,自腐蝕電壓正移0.416V。
(2)將微弧氧化技術(shù)和低表面能物質(zhì)OTMS表面修飾相結(jié)合,在TC4鈦合金表面構(gòu)建了具有微納米級粗糙結(jié)構(gòu)的超疏水膜層,水和腐蝕性離子難以侵入基底,從而使鈦合金具有優(yōu)異的長效耐腐蝕性能。與鈦合金基體相比,其腐蝕電流密度降低了近4個數(shù)量級,自腐蝕電壓正移動0.934V,且在3.5wt%的NaCl溶液中浸泡一周和在空氣中暴露一周后,自腐蝕電流密度仍能分別達到2.555×10-9A.cm-2和2.698×10-9A.cm-2。
參考文獻
[1] 王欣, 羅學(xué)昆, 宇波, 等. 航空航天用鈦合金表面 工程技術(shù)研究進展[J]. 航空制造技術(shù), 2022,65(04):
14-24. WANG Xin, LUO Xuekun, YU Bo, et al. Research progress on surface engineering technology of titanium alloy for aerospace[J]. Aeronautical Manufacturing Technology, 2022, 65 (04): 14-24. (in Chinese)
[2] 李永華, 張文旭, 陳小龍,等. 海洋工程用鈦合金研 究與應(yīng)用現(xiàn)狀[J]. 鈦工業(yè)進展,2022,39(01):43-48.
LI Yonghua, ZHANG Wenxu, CHEN Xiaolong, et al. Research and application status of titanium alloys for marine engineering[J]. Titanium Industry Progress, 2022, 39 (01): 43-48. (in Chinese)
[3] 廖贊, 繆衛(wèi)東, 馬嘉麗. 鈦合金在生物醫(yī)藥領(lǐng)域應(yīng)用 現(xiàn)狀和展望[J]. 新材料產(chǎn)業(yè), 2017,(03):19-24.
LIAO Zan, MIU Weidong, MA Jiali. Application status and prospect of titanium alloy in biomedical field[J]. Advanced Materials Industry, 2017, (03): 19-24. (in Chinese)
[4] CHEN Xiaowen, HU Jie, ZHANG Defen, et al. Study on corrosion resistance of TC4 titanium alloy micro‐arc oxidation/(PTFE+graphite) composite coating[J]. International Journal of Applied Ceramic Technology, 2022, 19(1): 397-408.
[5] 王東, 劉金玉, 孫世博, 等. 鎂合金表面微弧氧化/自組裝/鎳復(fù)合涂層的腐蝕過程和機理[J]. 中國表面工 程, 2024,37(01):100-109.
WANG Dong, LIU Jinyu, SUN Shibo, et al. Corrosion process and mechanism of micro-arc oxidation /self-assembly/nickel composite coating on magnesium alloy surface[J]. China Surface Engineering, 2024, 37 (01): 100-109. (in Chinese)
[6] 劉磊, 李來時, 吳玉勝, 等. 不同鋁合金基體黑色 微弧氧化膜的厚度對其結(jié)構(gòu)和性能的影響[J]. 中國表 面工程, 2023,36(06):163-177.
LIU Lei, LI Laishi, WU Yusheng, et al. The effect of the thickness of black micro-arc oxidation film on the structure and properties of different aluminum alloy substrates[J]. China Surface Engineering, 2023, 36(06): 163-177. (in Chinese)
[7] 毛政, 李洪, 張津, 等. TC4 鈦合金微弧氧化-溶膠 凝膠復(fù)合涂層的制備及其抗高溫氧化性能[J]. 中國表 面工程, 2015,28(03):76-81.
MAO Zheng, LI Hong, ZHANG Jin, et al. Preparation and high temperature oxidation resistance of micro-arc oxidation-sol-gel composite coating on TC4 titanium alloy[J]. China Surface Engineering, 2015, 28 (03): 76-81. (in Chinese)
[8] WANG Jing, FU Zhanghua, LIU Hao, et al. Preparation and characterization of micro-arc oxidation biological coatings on magnesium alloys containing graphene oxide[J]. Chemical Engineering Journal, 2024, 482: 149064.
[9] LI Huancai, YU Huijun, CHEN Chuanzhong, et al. Effect of graphene oxide on corrosion resistance and biological activity of micro arc oxidation ceramic layer on titanium alloy[J]. Materials Letters, 2022, 327: 133056.
[10] SHANG Wei, WU Fang, WANG Yuanyuan, et al. Corrosion resistance of micro-arc oxidation/graphene oxide composite coatings on magnesium alloys[J]. Acs Omega, 2020, 5(13): 7262-7270.
[11] CHEN Xiaowen, REN Peng, ZHANG Defen, et al. Corrosion and wear properties of h-BN-modified TC4 titanium alloy micro-arc oxide coatings[J]. Surface Innovations, 2022, 11(1-3): 49-59.
[12] LI Zhenwei, DI Shichun. The microstructure and wear resistance of microarc oxidation composite coatings containing nano-hexagonal boron nitride (HBN) particles[J]. Journal of Materials Engineering and Performance, 2017, 26: 1551-1561.
[13] GAO Yixiong, XIAO Shu, WU Hao, et al. Effect of h-BN nanoparticles incorporation on the anti-corrosion and anti-wear properties of micro-arc oxidation coatings on 2024 aluminum alloy[J]. Ceramics International, 2023, 49(23): 37475-37485.
[14] GUO Yufei, XU Luyao, Luan Junji, et al. Effect of carbon nanotubes additive on tribocorrosion performance of micro-arc oxidized coatings on Ti6Al4V alloy[J]. Surfaces and Interfaces, 2022, 28: 101626.
[15] YAZ1C1 S , MUHAFFEL F, BAYDOGAN M. Effect of incorporating carbon nanotubes into electrolyte on surface morphology of micro arc oxidized Cp-Ti[J]. Applied surface science, 2014, 318: 10-14.
[16] LIU Jiang, ZHU Xinhe, MA Dengqing, et al. Effect of nickel-coated carbon nanotubes on the preparation and wear resistance of microarc oxidation ceramic coating on ZL109 aluminum alloy[J]. Scientific Reports, 2022, 12(1): 11037.
[17] MARKOV M , PREVISLOV S , KRASIKOV A , et al. Study of the microarc oxidation of aluminum modified with silicon carbide particles[J]. Russian Journal of Applied Chemistry, 2018, 91: 543-549.
[18] DAI Ting, ZHAO Jie, YANG Xiaoyu, et al. Global and local corrosion performance of nano-SiC induced micro-arc oxidation coating on magnesium alloy[J]. Journal of Materials Engineering and Performance, 2022, 31(8): 6747-6758. [19] WANG Y Q, WANG X J, GONG W X, et al. Effect of SiC particles on microarc oxidation process of magnesium matrix composites[J]. Applied surface science, 2013, 283: 906-913.
[20] SHEN Yiding, FANG Kai, XIANG Yun, et al. Improvement in osteogenesis, vascularization, and corrosion resistance of titanium with silicon-nitride doped micro-arc oxidation coatings[J]. Frontiers in Bioengineering and Biotechnology, 2022, 10: 1023032.
[21] ALIOFKHAZRAEI M, ROUHAGHDAM A , GHOBADI E. Characterization of Si3N4/TiO2 nanocomposite coatings prepared via micro arc oxidation[J]. Journal of Nanoscience and Nanotechnology, 2011, 11(10): 9057-9060.
[22] GUO Lingyun, GAO Chunna WANG Fan, et al. Influence of content of silicon nitride nanoparticles into micro-arc oxidation coating of titanium on bactericidal capability and osteoblastic differentiation[J]. Surface and Coatings Technology, 2023, 458: 129346.
[23] NIE Wenxian, XIANG Mingzhe, Yu Leiting, et al. Self-lubricating micro-arc oxidized polytetrafluoroethylene composite coating on rivet steel for improve corrosion/wear resistance[J]. Materials Chemistry and Physics, 2023, 306: 128019.
[24] CHEN Jian, LI Wangning, XU Jinxin, et al. Effect of current density and polytetrafluoroethylene on the properties of micro‐arc oxide coating of pure aluminum[J]. International Journal of Applied Ceramic Technology, 2023, 20(5): 2860-2873.
[25] Kozelskaya A , Verzunova K , Akimchenko I , et al. Antibacterial calcium phosphate coatings for biomedical applications fabricated via micro-arc oxidation[J]. Biomimetics, 2023, 8(5): 444.
[26] ZHANG Xinxin, YANG Lei, LU Xueqin, et al. Characterization and property of dual-functional Zn-incorporated TiO2 micro-arc oxidation coatings: The influence of current density[J]. Journal of Alloys and Compounds, 2019, 810: 151893.
[27] BA Zhixin, WANG Yongmin, SUN Tianyi, et al. Preparation and properties of hydrophobic micro-arc oxidation/layered double hydroxide composite coating on magnesium alloy[J]. Surface and Coatings Technology, 2023, 475: 130113.
[28] 于浩洋, 孟建兵, 董小娟, 等. NiTi 合金微弧氧化 復(fù)合膜層的制備與性能[J]. 電鍍與涂飾, 2023,42(14):1-10.
YU Haoyang, MENG Jianbing, DONG Xiaojuan, et al. Preparation and properties of micro-arc oxidation composite coating on NiTi alloy[J]. Electroplating & Finishing, 2023, 42 (14): 1-10. (in Chinese)
[29] 莫格, 崔學(xué)軍, 張穎君, 等. AZ31B 鎂合金表面微 弧氧化/聚苯胺改性環(huán)氧涂層的腐蝕失效行為[J]. 中國 表面工程, 2020,33(02):37-46.
MO Ge, CUI Xuejun, ZHANG Yingjun, et al. Corrosion failure behavior of micro-arc oxidation / polyaniline modified epoxy coating on AZ31B magnesium alloy surface[J]. China Surface Engineering, 2020, 33(02): 37-46. (in Chinese)
[30] HE X, SONG R G, KONG D J. Microstructure and corrosion behaviours of composite coatings on S355 offshore steel prepared by laser cladding combined with micro-arc oxidation[J]. Applied Surface Science, 2019, 497: 143703.
[31] HUANG Niumeng, WANG Ying, ZHANG Yan, et al. Multifunctional coating on magnesium alloy: Superhydrophobic, self-healing, anti-corrosion and wear-resistant[J]. Surface and Coatings Technology, 2023, 463: 129539.
[32] 周塏杰, 辛蕾, 黃小文, 等. 鎂合金基底超疏水涂 層的制備及其防污防腐性能研究[J]. 材料保護,2023,56(05):71-75+126. ZHOU Kaijie, XIN Lei, HUANG Xiaowen, et al. Preparation of superhydrophobic coating on magnesium alloy substrate and its antifouling and anticorrosive properties[J]. Materials Protection, 2023, 56 (05): 71-75+126. (in Chinese)
[33] 楊文廣, 劉振紅, 朱梅婷, 等. 鋁合金表面超疏水 緩蝕自修復(fù)膜的制備及其耐蝕性[J]. 腐蝕與防護, 2021,42(05):1-7+37. YANG Wenguang, LIU Zhenhong, ZHU Meiting, et al. Preparation of superhydrophobic corrosion inhibition self-healing film on aluminum alloy surface and its corrosion resistance[J]. Corrosion & Protection, 2021, 42 (05): 1-7+37. (in Chinese)
[34] SHANG Wei, WANG Yuanyuan, WEN Yuqing, et al. Study on the properties of micro-arc oxidation self-assembled composite coatings on magnesium alloy[J]. International Journal of Electrochemical Science, 2017, 12(12): 11875-11891.
[35] MO Qiufeng, QIN Gemei, WEI Wu, et al. Hydrophobic composite layers for enhancing long-term corrosion resistance of Al alloy micro-arc oxidation coating[J]. Surface and Coatings Technology, 2022, 450: 128979.
[36] LIU Shimin, LI Baoe, LIANG Chunyong, et al. Formation mechanism and adhesive strength of a hydroxyapatite/TiO2 composite coating on a titanium surface prepared by micro-arc oxidation[J]. Applied Surface Science, 2016, 362: 109-114.
[37] WU Guolong, YIN Yanyi, ZHANG Shuo, et al. Effect of laser texturing on the antiwear properties of micro-arc oxidation coating formed on Ti-6Al-4V[J]. Surface and Coatings Technology, 2023, 453: 129114.
[38] WANG Ying, BAO Huayang, TANG Aiguo, et al. Ti3C2Tx-based composite coating on AZ31B Mg alloy surface for improved anti-corrosion/wear-reducing properties[J]. Materials Today Communications, 2023, 35: 105664.
作者簡介:王瑩,女,1982 年出生,博士,副研究員,碩士研究生導(dǎo)師。 主要研究方向為功能表面與功能涂層。 E-mail:ywang@cczu.edu.cn
相關(guān)鏈接